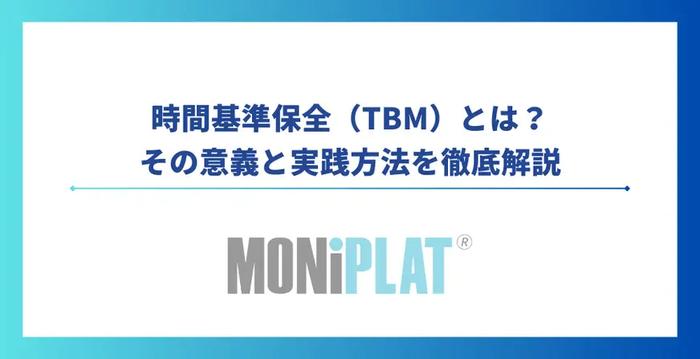
【2025年最新】時間基準保全(Time Based Maintenance:TBM)とは?その意義と実践方法を徹底解説
工場の現場での故障やトラブルは生産性を大きく低下させます。TBM(Time Based Maintenance)はこれらを未然に防ぎ、生産ラインの稼働率を安定化させるための効果的な方法です。
本記事では、TBMの意義やその導入方法について詳しく解説します。
時間基準保全(TBM)の基本概念
TBMを理解するには、その背景や役割を知ることが重要です。この章ではTBMの概要を解説します。
時間基準保全(TBM)の起源とその歴史
産業の歴史において、機械製造がはじまってしばらくの間、メンテナンスとは「設備が故障した段階で修理・修復する作業」と考えられていました。
しかし、それでは一度に多くの工程をストップさせてしまうことになります。大量生産時代に入ると、そのような方法では求められる生産性の向上に応えられないことがわかってきました。
このような経緯から、1950年代以降、信頼性工学[注1]の発達とともに、「トラブルが起きないように予防するために行う」という考え方に沿った設備保全である「予防保全」というコンセプトが注目されるようになりました。TBMは、その初期に登場した手法です。
時間基準保全(TBM)の定義とバスタブ曲線の関係
TBMは一定期間の使用後にオーバーホール[注2]や部品交換を行い、故障を未然に防ぐ手法です。その際に基準となっているのがバスタブ曲線の考え方です。
通常、設備が立ち上がった当初は稼働が安定せず不具合が発生することがありますが、その後は調整を施しながら安定状態に入ります。安定状態は永久的ではなく、しばらくすると部品の摩耗や疲労で再び異常や故障が生じます。
バスタブのような経緯曲線が由来
出典:[ 厚生労働省 / 職場のあんぜんサイト ]
これらの経緯を図で表すと、その形状が浴槽に似ていることから「バスタブ曲線」と呼ばれるようになりました。上記、図の中間にある安定期間(偶発故障期)に故障が発生することは稀です。
しかし、その裏で部品の摩耗や疲労は確実に進んでいます。そのため、この段階での保全活動が適切に行われれば、異常や故障の発生を抑え、設備やシステムの寿命を延ばせます。
日本における時間基準保全(TBM)のあり方
予防保全に対する研究は、機械製造の先駆者であるアメリカとイギリスがリードしていましたが、1960年代になると日本でも盛んになりました。1980年代に世界市場を席巻した日本製品の品質や生産性は、この成果に支えられたものと言えます。
また、高度成長期に建設された大型プラントも、半世紀以上が経過し、耐久性に不安を抱く関係者が増えています。設備の部分的な改修や補修、更新の必要性が高まる中、TBMが果たす役割はますます大きくなっています。
時間基準保全(TBM)は経済的合理性や持続可能性からも重要に
さらに現在、TBMの重要性は異なる視点でも語られています。万が一プラントで重大な事故が起きれば、企業は利益を損なうどころか致命的なダメージを受けかねません。
また、整備を怠って不良品を量産したり、無駄にエネルギーを消費すれば、環境への負荷が増大し、企業の社会的責任が問われます。設備の動作の確実性や健全性を維持するTBMの重要性は、こうした背景から一層高まっています。
- 製品やシステムなどの信頼性を高めるための技術や手法を研究する工学分野
- ひとつひとつの部品にまで分解・点検し、必要とされる洗浄や修理などの処置を行うこと
まとめ
時間基準保全(TBM)は、設備の定期的な点検と部品交換で故障を未然に防ぐ手法です。1950年代から予防保全として普及し、日本では品質向上と生産性向上に寄与しました。現在は環境負荷軽減や持続可能性の観点でも重要視されています。
時間基準保全(TBM)のメリット・デメリット
TBMは、課題解決のために生まれた手法で、多くのメリットをもたらします。しかし、条件や環境によっては、デメリットとなる場合もあります。
時間基準保全(TBM)のメリット
TBMには多くのメリットがあります。ここでは代表的なコスト、生産計画、働き方改善に関するメリットについて解説します。
コスト管理
決まった期日にオーバーホールや部品交換を行うことで、必要な費用を事前に算出でき、イレギュラーな出費を減らせます。これにより、コスト管理が容易になります。
また、パフォーマンスが不十分な状態で設備を稼働させ続けると、品質の低下や不良品の発生が懸念されます。取引先からの返品や不買、製品の廃棄により、利益を損なうだけでなく、検品や整理の手間も増え、余分な運用費用がかかります。TBMによって品質を保つことで、これらのコストを抑制できます。
計画的なメンテナンス
設備に異常や故障が生じると、ダウンタイム[注1]が発生します。異常や故障が複雑になるほど回復に時間がかかり、生産計画も崩れがちです。TBMは計画的なメンテナンスを実施することで、これらのリスクを軽減します。
さらに、メンテナンスを習慣化することで、点検漏れが減少し、従業員のメンテナンスに対する意識やスキルが向上します。
働き方改革
出典:[ 厚生労働省 / 2022年版ものづくり白書 ]
現在、社会全般で人手不足が問題視されており、製造業も例外ではありません。製造業の就業者数は、約20年間で157万人も減少しています。働き手を増やすことが難しい中で、これ以上の減少を防ぐには、働き方改革が必要です。
TBM導入前の現場では、予期せぬタイミングでの緊急対応が頻発し、担当者が退勤後や休日に呼び出されることもありました。TBMを導入することで、イレギュラーな勤務、残業や休日出勤が大幅に減少します。保全活動だけで全てが解決するわけではありませんが、働き方の改善に寄与する部分は大きいと考えられます。
時間基準保全(TBM)のデメリット
TBMのデメリットは、以下の3項目が挙げられます。
オーバーメンテナンスのリスク
TBMは一定の期間でメンテナンスを行うため、故障していない部品も交換することになります。その結果、コストがかかるという指摘もあります。
また、異常や故障が明確になった場合の対処に比べ、メンテナンスの工数が増えてしまうこともあります。このように「異常がない設備に対しても出費が生じる」「通常の作業に余分な労力をかける」といった点に不満を持つケースも少なくありません。
突発トラブルのリスク
TBMは一定の周期でメンテナンスを実施しますが、その間に突発的なトラブルが発生する可能性は残ります。
周期的なメンテナンスが行われていても、すべての異常や故障を未然に防ぐことは難しいためです。
担当者や設備・インフラの変更に弱い
初期のメンテナンス計画は、設備を提供したメーカーの指示や助言に基づいて決定されますが、その後は、設備の性質や製造環境、担当者の経験によって修正が行われます。
そのため、専任の担当者が他の部署に異動になったり、設備やインフラの仕様が変更された場合、それまでのやり方が機能せず、突発的な異常や故障が発生するリスクが高まることがあります。
- さまざまなトラブルで生産が停止してしまう時間のこと
まとめ
TBMのメリットは、計画的なメンテナンスによるコスト削減、生産計画の安定、働き方の改善です。一方、デメリットとして、オーバーメンテナンスによるコスト増や突発トラブルのリスク、担当者や設備変更時の管理の難しさが挙げられます。
時間基準保全(TBM)の実施方法と導入ステップ
TBMを実施するための具体的な方法とステップを紹介します。あくまでも一例なので、それぞれの設備や環境に合わせて内容をアレンジしてください。
設備のリストアップと優先順位付け
大小に関わらず、保全対象となる設備やその保全箇所、保全内容(分解、点検、洗浄、修正、部品交換など)をすべてリストアップします。
次に、それらを優先順位付けしていきます。この際、KY(危険予知)やRA(リスクアセスメント)といった判断基準を活用すると効果的です。たとえば、生産に深く関わり、ラインをストップさせる可能性がある設備は優先度を高く設定します。
一方で、電球の交換など、生産体制に影響が少ない設備は優先度を低く設定します。
メンテナンススケジュールの策定
設備のメーカー担当者からの仕様説明やマニュアルに加え、ユーザー自身のKY / RAの結果を基に、メンテナンスのスケジュールを策定します。これはTBMを実践する上で最も重要なポイントです。
たとえば、メーカーから「毎年分解点検を実施すること」が推奨されていても、設備停止が業務に与える影響が少ないと判断される場合、BM(事後保全)対応としてメンテナンスコストを抑える選択をすることもあります。
生産計画や人員配置など、関連する要素を考慮し、複数の設備が重なった場合は、上記の優先度をもとにメンテナンスの順序を決定します。
定期点検の記録と方法
TBMでは、点検や修理の履歴を設備管理台帳に詳細に記録しておくことが重要です。これにより、メンテナンス漏れを防ぎ、TBMのスケジュール調整や生産計画の立案に役立つ有益なデータを蓄積できます。
また、TBMと定期点検はほぼ同義であり、日常的な点検や定期的なメンテナンスもTBMの一部とみなされます。こうして、TBMを通じて定期的に設備の状態を確認し、異常や故障が発生する前に迅速かつ的確に対応することで、設備の寿命を延ばし、安定した生産体制を維持します。
まとめ
TBM導入は、設備リストと優先順位付け、メンテナンススケジュール策定、定期点検の記録が基本です。KY(危険予知)やRA(リスクアセスメント)を活用し、優先度に基づいて計画を立てることで、効率的な保全が可能になります。
他の保全手法との比較
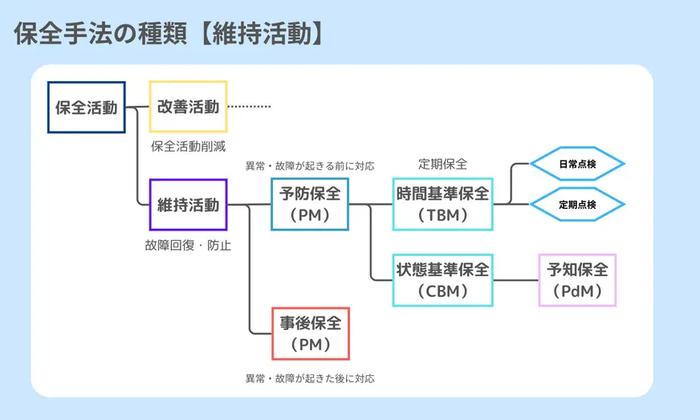
もう一つの予防保全(Preventive Maintenance:PM)、状態基準保全(Condition Based Maintenance:CBM)とは?
「トラブルが起きないよう予防するために行う」という考え方に基づく予防保全には、TBM以外にCBMという手法があります。
CBMは「状態基準保全」という名前の通り、設備の状態に基づいてメンテナンスを行う手法です。必ずしもリアルタイムで監視する必要はなく、TBMが時間基準に基づくのに対し、CBMは状態基準に基づくという点が重要です。
CBMは設備の状態を監視し、必要な時にのみメンテナンスを行うため、不要なメンテナンスを省け、結果的にTBMよりもコストを削減できる場合があります。強固なCBM体制を構築すれば、故障のリスクはTBMよりも低くなることが期待されますが、一般的にCBMには高いイニシャルコストと、場合によってはランニングコストもかかります。
そのため、CBMとTBMを効率よく併用するかどうかの判断は、設備の性質や環境、点検箇所などに加え、KY(危険予知)やRA(リスクアセスメント)といった基準に基づいて行われることが一般的です。
予知保全(Predictive Maintenance:PdM)とは?
予知保全とは、設備の状態を常に監視し、異常や故障の兆候を捉えて適切な対応をとる手法です。
ここでのポイントは、AIやIoTを取り入れた診断技術です。近年、これらの技術は飛躍的に進化し、異常や故障の予兆を捉える精度が大幅に向上しています。
最新のシステムの導入には高い初期費用がかかりますが、導入後は担当者の作業工数や部品交換などの手間やコストを軽減しつつ、小さなリスクも見逃さずに適切なメンテナンスが可能になるため、注目されている手法です。
事後保全(Breakdown Maintenance:BM)とは?
事後保全とは、設備に異常や故障が生じた後に修理や部品交換を行う手法です。TBMとは異なり、突発的なトラブルが発生した後に対応するのが事後保全の特徴です。
その結果、担当者が定時外の勤務を求められることもあり、交換用部品を保管する在庫スペースも必要です。そのため、事後保全は生産体制への影響が少ない場合や、大きなトラブルにつながらない、比較的規模が小さく、容易に対応できるメンテナンスに適しています。
まとめ
最適な保全手法は設備の特性や運用環境により異なりますが、生産安定性を重視するならTBM、効率と柔軟性を求めるならCBM、精密な予測が必要ならPdMが有効です。BMはコスト削減になるものの、故障リスクが大きいため影響の小さい設備に限定されます。
時間基準保全(TBM)導入の成功事例
企業にはさまざまな課題がありますが、それぞれの条件に合った方法でTBMを導入して解決した例はたくさんあります。
この章では、TBM導入による成功事例の一部を紹介します。
株式会社林田産業:保全情報の管理方法及び働き方を改善

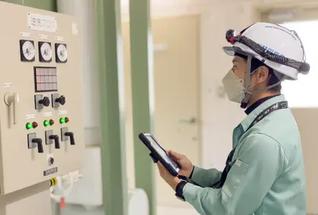
株式会社林田産業は、公共下水道処理施設の運営を受託しており、業務の一環として「微生物管理」を行っています。これには、各種機器設備の保全が不可欠です。同社はこれらの業務をデジタル化し、効率化を図りました。
紙の管理台帳をクラウドで管理できるシステムに移行し、現場ではスマートフォンで記録を行うようにしました。これにより、保全業務に必要な手間や時間が大幅に軽減されました。さらに、管理者への承認申請も電子メールで完了するため、労働時間の削減が実現しました。
株式会社デジック:定期保全をデジタル化でより正確かつ効率化
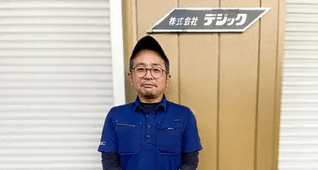
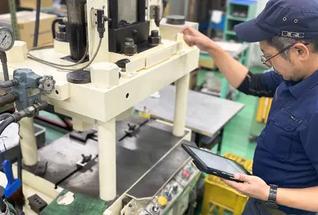
株式会社デジックは、パッキング製造および販売を主な事業としています。プレス機やクレーンなどの大きな設備から、ノギスや秤といった小型機器まで、大小さまざまな設備の定期保全が必要です。
取締役工場長の河合絢氏は、これらの保全管理をデジタルで行えるように改革を推進しました。すべての保全項目一覧がタブレットでわかりやすく把握でき、その結果を入力するだけで簡単に記録・保存が可能となりました。
紙の台帳を保存・整理する手間や時間、スペースが不要となり、担当者の意識も向上。保全業務に一段と力が入るようになりました。
まとめ
TBM導入の成功事例として、林田産業とデジックが保全業務をデジタル化。クラウド管理やスマホ・タブレットの活用により、作業効率と労働時間の大幅な改善を実現。紙の台帳が不要になり、担当者の意識も向上。保全業務のさらなる強化につながっています。
時間基準保全(TBM)導入時の注意点と課題
TBMは製造業に多くのメリットをもたらしますが、デメリットもあるため、実施前に確認しておくべき点がいくつかあります。この章では代表的なポイントを解説します。
保全項目が増える
TBMは、生産ラインが正常に稼働している場合でも、一定期間に決められた保全業務を遂行する必要があります。
そのため、生産体制や人員に余裕があるかを事前に確認しておくことが重要です。
コストがかかる
TBMでは、決められた期間内に部品交換を行うため、事後保全と比べてコストがかかることがあります。
企業にそのコスト負担の余裕があるかどうかを確認し、ある程度の期間にかかる費用をあらかじめ算出してキャッシュフローに組み込んでおくことが望ましいです。
スケジュールの変更に対応できるか
TBMと並行して事後保全も行っていたり、突発的な異常や故障が頻発した場合、トラブル解消が最優先されるため、TBMのスケジュールが守れなくなることがあります。
急なスケジュール変更に、どのように対応できるかを事前に考慮しておく必要があります。
まとめ
TBM導入には、保全項目増加でのリソース確認、部品交換コストの事前算出、急なスケジュール変更対応が重要です。特に、コスト負担や人員の確保を踏まえた柔軟な計画が成功の鍵となります。
時間基準保全(TBM)で設備の状態を維持し、生産性を向上させましょう
時間基準保全(TBM)は、設備を定期的に点検・メンテナンスすることで、設備の状態を良好に保ち、生産の安定化とコスト管理を実現する手法です。定期的な点検により設備の劣化を早期に発見し、適切な対応を行うことで、設備の信頼性を高めることができます。
TBM実践のポイント
- 設備のリスト化と優先順位付け:重要な設備を特定し、保全の優先度を設定
- スケジュールの策定:メーカーの推奨や運用状況に基づき、定期点検の計画を立案
- 定期点検の記録と活用:点検結果を詳細に記録し、次回以降の保全活動に活用
- デジタルツールの活用:保全情報をデジタル管理し、効率的な記録と情報共有を実現
TBMを導入することで、設備の状態を継続的に把握し、適切なメンテナンスが可能となります。設備の安定稼働を目指し、生産性の向上などを図る上で、TBMは欠かせない保全活動といえます。
時間基準保全(TBM)を始めるなら設備保全の一元管理に最適なMONiPLAT
TBMは設備の寿命を延ばし、コストを抑えながら安定した生産を可能にする手法です。特に、効率的なメンテナンス計画を立てることで、トラブルのリスクを最小限に抑えることができます。
MONiPLATは、設備保全に関するあらゆる情報を一元管理できるクラウドシステムです。端末に保全項目が一覧で表示され、結果を入力するだけで作業記録や管理者への報告書を簡単に作成できます。
さらに、MONiPLATでは、業務記録が自動で保存されるだけでなく、結果をグラフ化して状態変化を「見える化」することが可能です。これにより、さまざまなデータを活用した分析が柔軟かつ手軽に行えます。MONiPLATは、TBMを初めて導入する企業にも最適なツールです。ぜひ導入を検討してみてください。