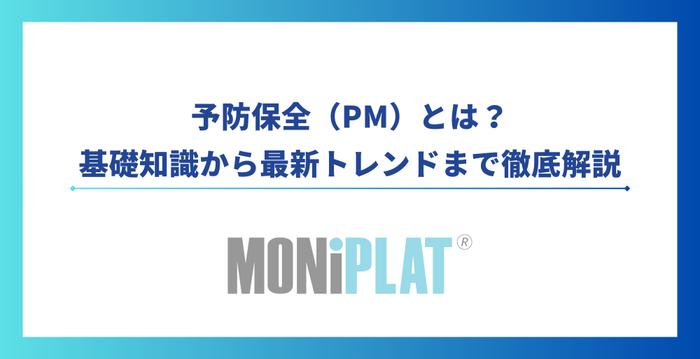
【2025年最新】予防保全(Preventive Maintenance:PM)とは?基礎知識から最新トレンドまで徹底解説
製造業において、生産設備や機械の異常や故障は、生産ラインの停止やコスト増加といった大きなリスクをもたらします。予防保全はそのリスクを未然に防ぎ、安定した稼働を実現する手法です。
本記事では、予防保全が誕生した背景や基本的な考え方から、TBMやCBMといった主要な手法、さらにIoTやAIを活用した最新の動向まで、総合的にわかりやすく解説します。予防保全を導入して設備管理を効率化し、生産性向上を目指す企業担当者の方は必見です。
予防保全(PM)の基本概念
予防保全を正しく理解するために、その背景や歴史、基本的な定義、重要性について詳しく見ていきましょう。
予防保全(PM)の起源と歴史
製造業において、初期の設備保全は事後保全が中心でした。設備や機械に異常や故障が発生した際に修理や部品交換を行うため、トラブルが発生するたびに生産ラインが停止し、工程全体に大きな影響を与えていました。
しかし、大量生産時代に入ると、生産効率の向上が求められる中で「故障してから対処する」という後手の対応では対応しきれなくなりました。そこで1950年代以降、設備の異常や故障を未然に防ぐことを目的とした「予防保全」の考え方が登場し、注目を集めるようになったのです。
予防保全の導入を契機に、計画的なメンテナンスとしてTBMが普及しました。その後、設備の状態に応じたCBMやデータを活用して予測する予知保全など、さまざまな保全手法が発展していきました。
予防保全(PM)の定義と特徴
予防保全は設備や機械が故障する前に、寿命や劣化状況を予測し、計画的に点検やメンテナンスを行う手法です。
JIS(日本産業規格)では、予防保全を次のように定義しています。
故障に至る前に寿命を推定して,故障を未然に防止する方式の保全
製造現場では、静止機器(タンクや釜)や回転機器(モーターやコンプレッサ)、配管ライン、計測・制御機器など、多種多様な設備が稼働しています。これらの機器を安定して運用し、トラブルを防止するために、専門の保全部門が計画的に点検・整備を行う活動が「予防保全」です。
予防保全の最大の特徴は「故障を未然に防ぐ」ことで、設備の停止や生産計画の遅延を最小限に抑える点です。これにより設備の寿命を延ばし、製品の品質維持やコスト削減にも貢献します。
ちなみに予防保全と似た言葉に計画保全(Planned Maintenance)がありますが、両者には明確な違いがあります。
計画保全とは、設備や機械の故障を未然に防ぐために、計画的に点検・修理・部品交換などの保全活動を行う総合的な管理手法を指します。その中で予防保全は、計画保全の一部に位置づけられ、故障の兆候を事前に察知し、設備が停止する前にメンテナンスを行う手法を指します。
つまり、計画保全は大きな枠組みであり、その中に予防保全や事後保全といった複数の手法が含まれます。この違いを理解することで、設備の状態や運用環境に応じた適切な保全手法の選択が可能となり、生産性向上やコスト削減につなげることができます。
出典:[ JIS(日本産業規格) / 2021生産管理用語 ]
予防保全(PM)の目的と重要性
予防保全の目的は、設備や機械の異常や故障を未然に防ぎ、安定した生産活動を維持することです。そのためには、適切なタイミングで点検や部品交換を実施することが重要になります。
点検やメンテナンスが早すぎると、まだ十分に使用できる部品を交換してしまう「オーバーメンテナンス」の状態になり、無駄な作業やコストの増加を招く可能性があります。一方で対応が遅れると、故障や異常の兆候を見逃し、生産ラインの停止や製品品質の低下につながりかねません。
予防保全を適切に実施することで、設備のトラブルを未然に防ぐだけでなく、ダウンタイムを削減し、計画的な生産スケジュールの遂行が可能になります。また設備や機械の劣化を早期に発見して対処することで、故障の進行を防ぎ、結果として設備寿命の延長や保全コストの最適化にもつながります。
このように、予防保全は「生産性の向上」と「設備の長寿命化」という2つの側面から、製造現場において重要な役割を果たしています。
まとめ
予防保全は設備や機械が故障する前に計画的な点検やメンテナンスを行う手法です。1950年代に登場し、生産効率向上のために広まりました。主な目的は故障の未然防止と生産性の維持であり、適切なタイミングでメンテナンスを実施することで設備の寿命延長やコスト削減にもつながります。計画保全の一部として位置づけられ、現場の安定稼働に欠かせない役割を果たしています。
予防保全(PM)のメリット・デメリット
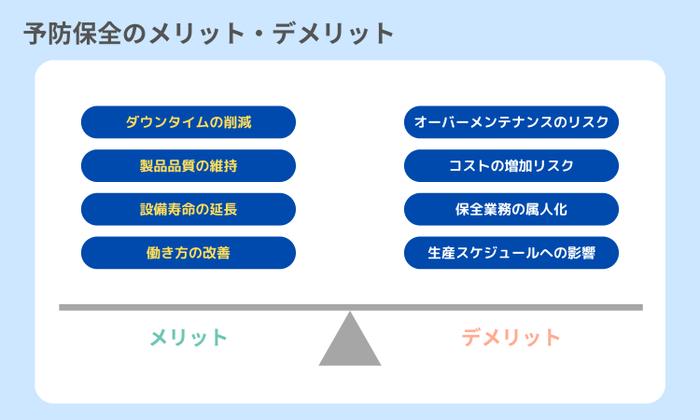
予防保全を導入することで、製造現場にさまざまなメリットがもたらされますが、一方で運用において注意すべきデメリットも存在します。この章では、予防保全の両面について解説します。
予防保全(PM)のメリット
予防保全にはさまざまなメリットがあります。以下でそれぞれについて解説します。
ダウンタイムの削減
設備や機械が故障すると、復旧までの時間(ダウンタイム)が発生し、生産が停止します。
予防保全は異常や故障の兆候を事前に察知してメンテナンスを行うため、突発的なトラブルを減少させ、生産スケジュールの遅延を防ぎます。これにより生産効率を安定的に維持することが可能です。
製品品質の維持
設備の劣化や不具合は製品の品質にも影響します。予防保全により設備を常に良好な状態に保つことで、生産された製品の品質低下を防ぎ、一定のクオリティを維持することができます。
設備寿命の延長
設備や機械は稼働に伴い部品が摩耗・劣化しますが、適切なタイミングで点検・修理を行うことで故障を未然に防ぎ、設備全体の寿命を延ばすことができます。設備の長寿命化は新規投資のコスト削減にもつながります。
働き方の改善
予防保全は突発的な故障や緊急対応を減らすため、担当者の残業や休日出勤の発生を抑えることが可能です。また重大な設備トラブルを防ぐことで、作業現場の安全性向上にも寄与し、従業員の安心・安全な労働環境を実現します。
予防保全(PM)のデメリット
予防保全には以下のようなデメリットも伴います。
オーバーメンテナンスのリスク
予防保全は定期的な点検や交換を行うため、まだ使用可能な部品を早期に交換してしまうことがあります。これを「オーバーメンテナンス」と呼び、無駄な作業やコスト増加を招くリスクがあります。そのため、メンテナンス周期や対象範囲を適切に設定することが重要です。
コストの増加
予防保全には部品交換や点検作業に伴う費用が発生します。特に新しいシステムや高度な技術を導入する場合、初期費用や運用コストが大きくなることがあります。
企業の予算に合わせて、長期的な投資対効果(ROI)を見極めた導入が求められます。
保全業務の属人化
CBMや予知保全など、高度な予防保全手法では、専門知識や技術が必要になります。そのため、特定の担当者に業務が集中する属人化が発生しやすくなります。
緊急時の対応や後任への引き継ぎが困難になることを避けるため、知識や技術の標準化と共有が不可欠です。
生産スケジュールへの影響
予防保全は保全計画に基づいて点検や修理を行うため、生産計画や人員計画との調整が必要になります。
また、突発的な故障が発生すると、優先対応により予防保全のスケジュールが後回しになることもあります。予防保全と事後保全を適切に組み合わせ、柔軟な対応ができる体制を整えることが重要です。
まとめ
予防保全は設備の故障を未然に防ぎ、生産の安定稼働や品質維持に貢献します。一方で、定期的なメンテナンスが必要なため、過剰な部品交換によるオーバーメンテナンスや、運用コストの増加といった課題も存在します。これらを踏まえ、計画的で柔軟な保全体制が重要です。
予防保全(PM)の種類と特徴
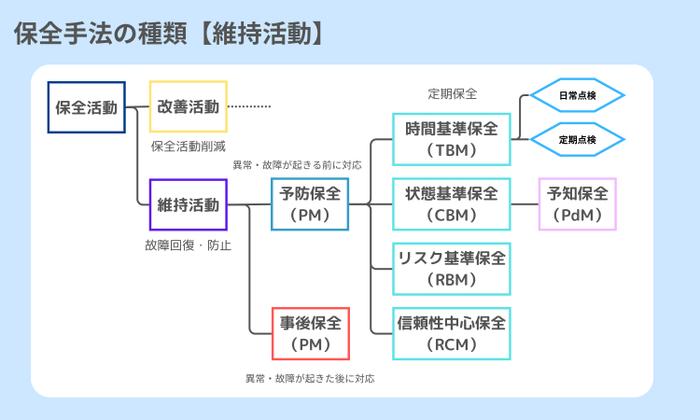
予防保全には複数の保全手法があり、それぞれ「検査や部品交換をどのタイミングで行うか」に特徴があります。以下で主な種類とその概要を解説します。
時間基準保全(Time Based Maintenance:TBM)
TBMは、設備の状態に関わらず「一定の時間や期間」を基準に保全作業を行う手法です。定期的にメンテナンスを実施することで故障のリスクを抑えますが、まだ使える部品を交換してしまう「オーバーメンテナンス」の可能性があるため、コスト管理が重要です。
詳細は以下「時間基準保全(TBM)とは?」の記事をご覧ください。
状態基準保全(Condition Based Maintenance:CBM)
CBMは設備や機械の状態をモニタリングし、特定の基準に達したタイミングで保全を行う手法です。
たとえば部品の摩耗や温度の上昇などを基準にメンテナンスを実施します。不要な作業を減らせる反面、設備の状態を正確に把握するためには専門的な知識や高度な技術が必要です。
詳細は「状態基準保全(CBM)とは?」の記事をご覧ください。
予知保全(Predictive Maintenance:PdM)
予知保全はIoTやセンサーを活用して設備の状態をリアルタイムで監視し、データ分析によって故障や異常の発生を予測する手法です。
AIや機械学習を用いることで、より高精度な予測が可能になります。導入コストは高めですが、メンテナンス効率の向上やリスク低減が期待できます。
詳細は「予知保全(PdM)とは?」の記事をご覧ください。
リスク基準保全(Risk-Based Maintenance:RBM)
リスク基準保全は、設備や機械に異常や故障が発生した場合の影響度と発生確率を評価し、優先度に応じてメンテナンスを行う手法です。石油化学プラントや大型製造設備など、リスク管理が重要な業界で広く導入されています。
あらかじめリスクアセスメントを実施し、設備ごとのリスクの大きさを数値化することで、限られたリソースを効率的に配分しながら保全計画を立てることができます。
トラブルが発生した際の影響度が大きい設備を優先して保全するため、コストの最適化が図れます。その一方で、リスク評価の精度が求められるため、専門知識や経験、評価ツールの活用が不可欠です。
信頼性中心保全(Reliability-Centered Maintenance:RCM)
RCMは設備や機械の「機能維持」と「信頼性向上」を目的とした保全手法です。特に航空産業や高度な生産設備を要する業界において、設備の効率的な運用と寿命延長に貢献する重要な手法となっています。
設備ごとに故障の影響度や故障モード[注1]を分析し、最適な保全方法を選定することで、リスクとコストのバランスを最適化します。重要度の高い設備や機器に対して、最適な保全手法を組み合わせて適用。さらに故障の予防だけでなく、稼働率の最大化と運用コストの削減を実現します。
- 故障状態の形式による分類。断線、短絡、折損、摩耗、特性の劣化など
その他の予防保全手法
予防保全には、特定の設備や運用環境に合わせて適用される手法も存在します。
たとえば、利用基準保全(Usage-Based Maintenance:UBM)は設備や機械の稼働量や使用回数を基準として、検査や部品交換を行う手法です。稼働率が不均一な設備に適しており、利用状況に応じた柔軟な保全が可能です。
また、故障発見保全(Failure Finding Maintenance:FFM)は非常用設備やバックアップ装置など、通常時には稼働しない機器に対し、定期的な点検や稼働確認を行うことで故障を発見し、メンテナンスを行う手法です。
これらの手法は、一般的な予防保全に比べると適用範囲が限定的ですが、設備の特性や業務内容に応じて効果的に活用されることがあります。
まとめ
予防保全は、設備や機械の故障を未然に防ぐために「点検や部品交換のタイミング」に応じた手法が選ばれます。各手法はコスト管理や技術導入とのバランスが重要であり、設備の特性に合わせた最適な選択が保全効率の向上につながります。
予防保全(PM)以外の保全方法
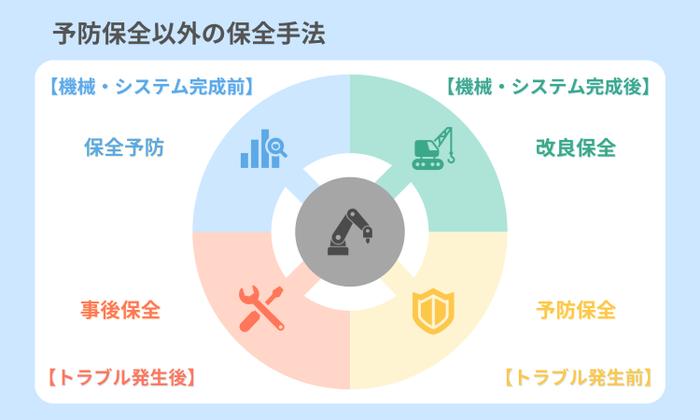
保全手法は、設備の状態や運用段階に応じて異なるアプローチやタイミングで実施されます。この章では、予防保全以外の保全手法について、それぞれの目的や特性について解説します。
事後保全(Breakdown Maintenance:BM)との違い
事後保全は、設備や機械が故障してから修理や部品交換を行う保全手法です。定期的な点検やメンテナンスは行わず、設備の状態を常に運用し続けることで日常の保全コストを抑えられるメリットがあります。しかし、故障が発生した際には生産活動が停止し、復旧作業や交換部品の確保に時間やコストがかかるリスクも伴います。
予防保全が計画的なメンテナンスで故障を未然に防ぐのに対し、事後保全はあくまで「後手の対応」であり、突発的なトラブルの発生に左右されやすい手法です。そのため、生産ラインへの影響が少ない設備や軽微なトラブルで済む機械に対して適用されることが一般的です。
詳細は「事後保全(BM)とは?」の記事をご覧ください。
保全予防(Maintenance Prevention:MP)との違い
保全予防は設備や機械の計画・設計段階から保全の視点を取り入れ、故障や異常が発生しにくい状態をあらかじめ作り込む保全手法です。過去の保全実績やデータをもとに、設計段階でトラブルの原因となる要素を予測し、それを排除するための対策を盛り込むことで、完成後の保守作業の手間やコストを軽減します。
この手法は、特に新規設備やシステムの導入時に有効であり、設備自体の耐久性や操作性を高めることが可能です。たとえば、部品の材質や構造を最適化することで摩耗を抑えたり、点検がしやすい設計を取り入れることで、運用後の保全効率を大幅に向上させることができます。
一方で、保全予防を実施するには設計段階での綿密な計画と予測が必要です。そのため、既存設備に対しては適用しづらく、あくまで新設計の設備に限られる手法となります。
改良保全(Corrective Maintenance:CM) との違い
改良保全はすでに運用されている設備や機械に対して、異常や故障が発生しにくいように構造や性能を改善することを目的とした保全手法です。設備の保守作業だけでなく、故障や生産効率低下の根本原因を解消するための改良を行う点が特徴です。
具体的には、部品の材質を耐久性の高いものに変更したり、構造設計を見直して故障の発生しにくい仕組みにするなどの取り組みが含まれます。また稼働条件を改善して設備の負荷を軽減したり、サイクルタイムの短縮による生産効率の向上を図ることも改良保全の一環です。
このように、改良保全は予防保全を補完し、長期的な視点で設備の安定稼働や保全コストの削減に貢献します。しかし、改良作業には一時的な設備の停止や追加のコストが必要になるため、実施のタイミングや改善内容の優先順位を慎重に検討する必要があります。
まとめ
予防保全以外の保全手法は、設備の状態や導入段階に応じて異なるアプローチを取ります。保全の目的や実施タイミングによって使い分けることで、設備の安定稼働とコスト最適化が可能になります。設備の状態や運用環境を考慮し、最適な保全手法を選ぶことが重要です。
予防保全(PM)の実施方法とステップ
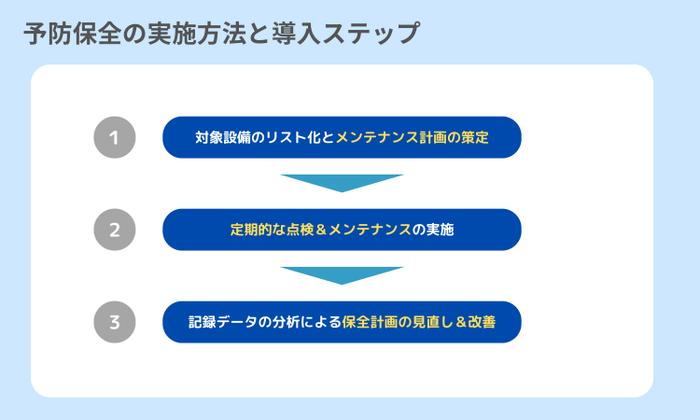
予防保全を効果的に導入・運用するためには、計画から実行、改善までを段階的に進めることが重要です。この章では、実施手順を3つのステップに分けて解説します。
保全計画の策定
予防保全の第一歩は、対象設備のリスト化とメンテナンス計画の策定です。
- 対象設備と部品のリスト化
- メンテナンススケジュールの作成
- 管理ツールの準備
まず保全対象となる設備や機器をリストアップし、それぞれの部品ごとに点検や交換が必要な箇所を明確にします。設備の稼働状況や使用期間を考慮し、具体的な基準(「〇時間稼働ごと」や「1年ごとに部品交換」など)を設定することがポイントです。
次に、設備ごとの点検周期やメンテナンス内容に基づいてスケジュールを作成します。作業の担当者や実施タイミングを決めることで、計画的な保全活動が可能になります。
最後に、保全の進捗や履歴を管理するためのツールや台帳を用意します。デジタル管理システムを導入すれば、作業の「済/未」や履歴情報を一元化でき、効率的な運用が実現します。
点検・メンテナンスの実施
次に保全計画に基づき、定期的な点検とメンテナンスを実施します。
- 計画に沿った点検の実施
- メンテナンス結果の記録
- 設備の状態把握と改善点の特定
計画されたスケジュールに従い、対象設備の点検や洗浄、修正、部品交換を行います。作業時にはチェックリストや管理台帳を活用し、作業漏れを防ぎましょう。
メンテナンスが完了したら、点検結果や修理内容を正確に記録します。いつ、どの箇所で、どのような作業を行ったのかをデータとして残すことで、保全の履歴管理や次回のメンテナンス計画に役立てることができます。
また点検中に発見した設備の不具合や摩耗状況を把握し、必要に応じて改善点を洗い出します。早期に劣化や異常の兆候を捉えることで、設備の長寿命化や予期せぬトラブルの防止につながります。
データ分析とフィードバック
点検データを活用し、保全計画の見直しや改善を行います。
- 記録データの分析
- 保全計画の見直し
- 保全方法のステップアップ
点検やメンテナンスで収集したデータを分析し、設備の状態や劣化傾向を把握します。「点検の頻度は適切か?」や「無駄なメンテナンスはないか?」などの観点で、保全活動の効果を客観的に評価しましょう。
分析結果をもとに、必要に応じて保全計画を見直します。たとえば、点検周期を最適化することでオーバーメンテナンスを防ぎ、効率的な運用が可能になります。
さらに、データから得られた知見を活かして保全方法の改善やステップアップを検討します。TBMからCBMへ、さらには予知保全への移行を視野に入れることで、設備保全の精度と効率を一層高めることができます。
まとめ
予防保全を効果的に実施するには、計画の策定、点検・メンテナンスの実施、データ分析と改善の3つのステップが重要です。これらのステップを循環させることで、保全の継続的な改善と運用効率の向上が実現します。
予防保全(PM)の導入事例
予防保全を実践することで、設備のダウンタイム削減やコスト最適化に成功した企業は多く存在します。当社の設備保全システム「MONiPLAT」を活用した導入事例をご覧いただくことで、予防保全の実際の効果や具体的な活用イメージを掴んでいただけます。
MONiPLATの導入事例はこちらから
IoT・AIで進化する予防保全(PM)の最新動向
近年、設備保全の分野ではIoTやAIなどの先端技術が注目されており、予防保全のあり方も大きく変わりつつあります。デジタル技術の導入により、設備管理の精度向上や効率化が進む中、今後どのような進化が期待されるのでしょうか。
データの収集・分析の高速化
IoT技術の発展により、センサーや機器からリアルタイムで設備の状態データを収集し、AIを活用して即座に解析できるようになりました。従来は手作業で行っていたデータ収集や分析も自動化され、異常や故障の兆候を早期に検知するスピードと精度が飛躍的に向上しています。
今後、さらに技術が進化すれば、データの高度な解析や予測が可能となり、故障や異常を未然に防ぐだけでなく、生産効率の最適化にも貢献することが期待されています。
業務の効率化とコストダウン
IoTとAIを活用することで、設備の状態監視からメンテナンスの判断までを自動化できるため、保全業務にかかる労力や時間を大幅に削減できます。
これにより、以下のような効果が見込まれます。
- メンテナンスのタイミング最適化による、オーバーメンテナンスの防止
- 故障や異常を未然に防ぐことで、ダウンタイムを最小化
- 効率的な保全業務により、メンテナンスコストや人件費の削減
効率化とコスト最適化が同時に実現することで、経営資源を他の重要な業務へ振り向ける余裕も生まれます。
既存設備への対応と延命化
IoT技術の柔軟性を活かせば、老朽化した設備にもセンサーや計測機器を後付けすることで、CBMや予知保全を実現できます。
具体的には、以下のような効果が期待されます。
- 老朽化した設備の状態を常に監視し、適切なタイミングでメンテナンスを実施
- 故障のリスクを低減し、設備の耐用年数を延長
- 既存設備への投資効率を最大化し、新規設備投資の抑制
これにより、限られた予算でも設備の運用効率と寿命を大幅に改善することが可能です。
持続可能な開発目標(SDGs)との関連性
IoT・AI技術を活用した予防保全は、SDGs(持続可能な開発目標)の達成にも貢献します。
たとえば、以下の目標との関連が考えられます。
- 「8. 働きがいも 経済成長も」:保全業務の効率化により、働き方改革を推進し、生産性と従業員満足度を向上
- 「9. 産業と技術革新の基盤をつくろう」:デジタル技術を活用したスマート保全体制を構築し、設備管理の高度化とイノベーション創出を支える
- 「12. つくる責任 つかう責任」:設備の状態管理を徹底することで、不要な部品交換や廃棄物を削減し、資源の無駄を防止
このように、IoTやAIの活用による予防保全は、設備管理の最適化だけでなく、持続可能な社会の実現にも貢献する重要な要素です。
まとめ
IoTやAIの導入により、予防保全は大きく進化しています。リアルタイムでデータを収集・解析できる技術が発展したことで、故障や異常の兆候を迅速かつ高精度に検知し、未然に防ぐことが可能となりました。さらに設備寿命の延長や新規投資の抑制や、SDGsへの貢献にも寄与しています。
予防保全で設備の故障を未然に防ぎ、生産性を最大化しよう
予防保全は設備や機械が故障する前に適切なメンテナンスを実施し、生産の安定稼働やコスト最適化を実現する手法です。IoTやAIの進化により、保全の精度や効率が向上し、持続可能な運用も可能になっています。
予防保全実践のポイント
- 計画的な保全体制の構築:設備のリスト化と点検スケジュールの策定
- データ収集と分析の徹底:保全履歴を記録し、状態を正確に把握
- 適切な保全手法の選定:設備特性に応じたTBMやCBM、予知保全などの活用
- 柔軟な保全改善の推進:データを基に計画を見直し、効率化を図る
予防保全を実践することで、設備の故障を未然に防ぎ、生産性向上やコスト削減、労働環境の改善が可能です。さらにIoTやAIの活用により、既存設備の延命や持続可能な社会への貢献も期待できます。計画的な保全活動を継続し、設備管理の最適化を実現しましょう。
予防保全(PM)を始めるなら設備保全の一元管理に最適なMONiPLAT
予防保全を効果的に実施するためには、設備情報の一元管理とメンテナンスの効率化が欠かせません。MONiPLATは、設備保全に関するあらゆるデータをクラウド上で一元管理し、予防保全の計画から実施、改善までを強力にサポートするシステムです。
MONiPLATには、TBMとCBM の両方の機能が組み込まれており、予防保全のさまざまな手法に柔軟に対応可能です。
TBMは20設備まで無料でご利用いただけます。予防保全の第一歩として、まずはMONiPLATを活用して効率的な設備管理を始めてみませんか?