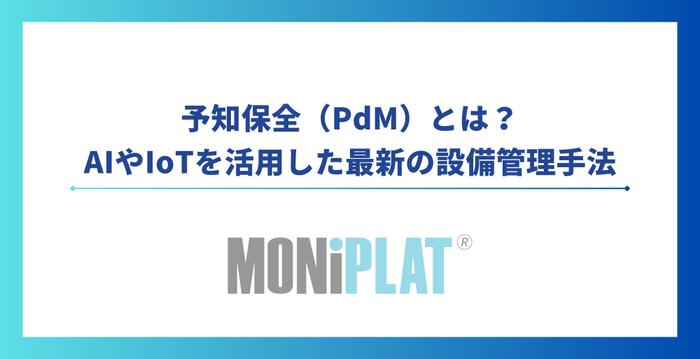
【2025年最新】予知保全・予兆保全(Predictive Maintenance:PdM)とは?AIやIoTを活用した最新の設備管理手法
これまでにさまざまな手法が進化してきた保全業務は、現在、IoTやAI、機械学習の発展により、大きな変革を迎えています。その中心にあるのが、これら先進技術を活用した予知保全(Predictive Maintenance:PdM)です。
予知保全では、IoTセンサーやビッグデータ分析、AI予測モデルを活用して設備の状態をリアルタイムに監視し、異常や故障を事前に予測することで、最適なメンテナンスのタイミングを判断します。これにより、予期しないダウンタイムの削減や生産性の向上が期待でき、設備保全にかかるコストの最適化が可能です。従来の保全手法に比べて、より精度が高く、効率的なメンテナンスを実現します。
本記事では、次世代のメンテナンス手法として注目される予知保全および予兆保全の特徴や導入のポイントについて詳しく解説します。
予知保全・予兆保全(PdM)の基本概念
予知保全は、最新のテクノロジーを駆使した新しい保全手法であり、異なる理解がされることもありますが、現在ではおおむね以下のように定義されています。
予知保全(PdM)の起源と歴史
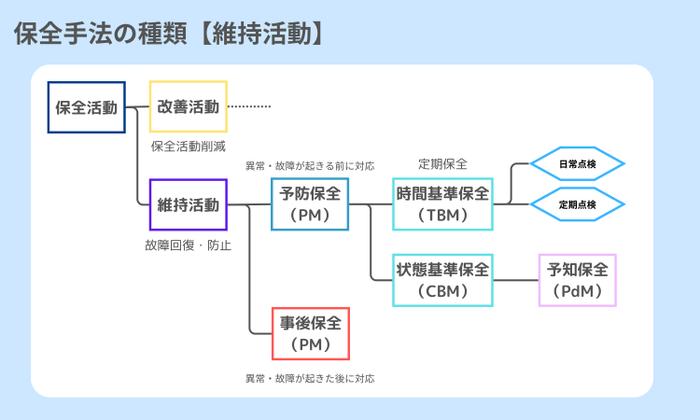
保全業務は当初、設備や機械に異常や故障が発生した後に対処する「事後保全(BM)」から始まりました。
しかし、この方法では予期せぬダウンタイムが頻繁に発生し、生産性が大きく損なわれるという問題がありました。特に、19世紀から20世紀初頭にかけての大量生産の時代に、この問題は顕著になりました。
その解決策として、1920年代にアメリカで「予防保全(PM)」が提唱されました。予防保全の一環として、決まった期間ごとに点検や修理を行う「時間基準保全(TBM)」、さらに、機械や設備の状態を監視して必要なタイミングでメンテナンスを実施する「状態基準保全(CBM)」が考案されました。
予知保全は、この状態基準保全をさらに進化させたもので、2020年代に入ってからIoTやAI、機械学習などの先進技術の発展により、実用化が進んでいます。これにより、より精度の高い予測と効率的なメンテナンスが可能になりました。
予知保全(PdM)の定義と特徴
予知保全はCBMの発展とされ、日本産業規格(JIS)では「状態基準保全」と同義として扱われています。CBMと同様に、設備や機械の状態をIoTセンサーでリアルタイムに監視しますが、AIや機械学習を活用する点で異なります。
これにより、過去のデータや運用履歴を用いた予測モデルを構築し、より精度の高い微細微細な異常や故障の兆候を事前に察知します。この手法により、メンテナンスのタイミングを最適化し、無駄な点検や過剰なメンテナンスを防ぎつつ、設備の寿命を最大化することが可能です。今後、これらの技術がさらに進化することで、予知保全の精度は一層向上することが期待されています。
なお、「予知保全」と「予兆保全」はほぼ同義語として使われており、両者に大きな違いはありません。
予知保全(PdM)の目的と重要性
保全業務の使命は、言うまでもなく円滑な生産活動のために、設備や機械をメンテナンスすることです。
しかし、最近では「設備や機械を長く安全に使い続けられるようにすること」も重要な目的になっています。設備や機械には耐用年数がありますが、扱い方によっては長く使用できます。また、高度経済成長期に導入した設備や機械も、なるべく負担をかけなければ、まだまだ現役で活躍することができます。
企業にとって、設備や機械の使用期間を延ばすことはコスト的に大きなメリットがあります。予知保全は、これまでに生まれた保全業務のなかで、もっともその役割を果たすことができると見られています。
まとめ
予知保全はIoTやAIを活用し、設備や機械の状態をリアルタイムで監視・予測する先進的な保全手法です。CBM(状態基準保全)の発展形として、データを基に異常や故障を未然に察知し、最適なメンテナンスを実現します。これにより設備寿命を延ばし、コスト削減や生産性向上を可能にします。特に持続可能な設備管理の重要性が求められる現代において、予知保全は欠かせないアプローチです。
予知保全(PdM)のメリット・デメリット
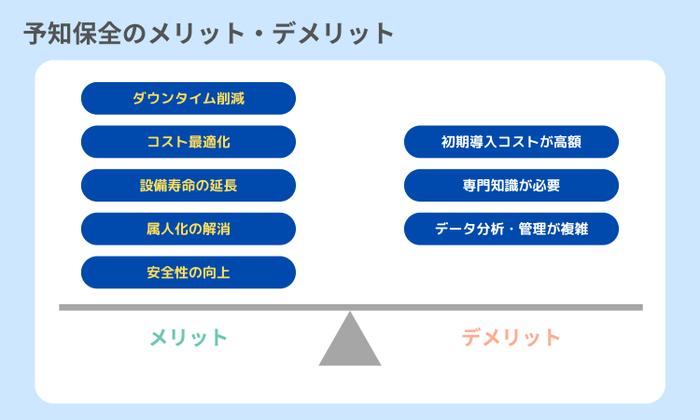
予知保全はこれまでの保全手法と比べて、革新的なアプローチを提供します。
しかし、最新技術を活用するため、必ずしもすべての現場に適しているわけではありません。この章では、そのメリットとデメリットを整理して解説します。
予知保全(PdM)のメリット
予知保全には、以下のような特徴的なメリットがあります。各ポイントを5つのカテゴリに分けて説明します。
異常や故障の早期発見によるダウンタイム削減
設備の状態をリアルタイムでモニタリングし、異常予兆を早期に検知するため、故障が発生する前に予防的な対策が可能です。このアプローチにより、計画的なメンテナンスが実施でき、突発的なダウンタイムの発生を防ぎます。
これにより、生産スケジュールの安定化や、設備の稼働率向上が期待できるほか、長期的なコスト削減にもつながります。
- 予防的なメンテナンスを実施し、ダウンタイムを削減
- 生産計画の安定化に寄与し、顧客満足度向上を実現
メンテナンスコストの削減と最適化
予知保全では設備の実際の状態に基づいてメンテナンスを行うため、不要な作業を省くことが可能です。これにより、無駄な部品交換を減らし、コストの最適化が実現できます。
- 必要な部品交換やメンテナンスのみを実施し、過剰な作業を回避
- 在庫管理の効率化により、在庫過多や欠品リスクを低減
設備寿命の延長と資産効率の向上
設備の状態を正確に把握することで、適切なメンテナンスが可能になり、設備の寿命を延ばすことができます。これにより、設備への投資効果が最大化され、資産効率が向上します。
- 劣化を早期に発見し、適切なタイミングでのメンテナンスを実施
- 長期間にわたり設備の性能を安定的に維持
保全業務の属人化の解消とデータ活用
IoTデバイスやAIによるデータ分析を活用することで、担当者の経験に依存しない保全体制が構築できます。これにより、属人化を解消し、組織全体の保全品質を均一に保つことが可能です。
- データドリブンな意思決定が可能となり、保全計画の精度が向上
- データの蓄積により、故障パターンの解析やメンテナンス計画の改善が可能
安全性の向上とリスクの低減
設備の異常を早期に発見することで、重大事故を未然に防ぎ、安全性を確保します。これにより、法的規制の遵守や従業員の安全確保が容易になります。
- リスクを早期に検知し、重大事故の発生を防止
- 作業員の安全性を高め、法的基準への対応を支援
予知保全(PdM)のデメリット
予知保全は多くのメリットを持つ一方で、導入や運用における課題もあります。以下に、主なデメリットを整理しました。
初期導入コストの高さ
高度なセンサーやモニタリングシステムを導入するための初期費用がかかります。また、既存のシステムやインフラとの統合には追加コストが生じる可能性があります。
- 新規設備やシステム導入の費用負担
- システム統合や運用コストの継続的な管理が必要
専門知識とスキルの必要性
予知保全がスタートすれば、誰もが「設備や機械の状況を客観的に把握すること」が可能になりますが、そのためのシステムの構築にはIoTやAIなどの専門知識や技術が不可欠です。
システムが稼働した後も調整や変更など、運用を継続するためのスキルが求められます。
データ管理と分析の難易度
予知保全は大量のデータを収集・分析して精度を高める必要があります。これにはデータ管理のシステムや適切な分析手法が求められ、失敗すると正確な予測が困難になります。
- 大量のデータ管理が複雑で、クラウドインフラやセキュリティの整備が必要
- 異常データの解釈や分析の難易度が高く、経験と判断力が求められる
まとめ
予知保全は異常や故障の早期発見によるダウンタイム削減、メンテナンスコストの最適化、設備寿命の延長など、多くのメリットをもたらす先進的な保全手法です。一方で、初期導入コストの高さや専門知識の必要性、大量データの管理と分析の難易度などの課題も伴います。導入の際にはこれらの利点と課題を考慮し、自社の状況に合わせた活用計画を立てることが重要です。
予知保全(PdM)の実施方法と導入ステップ
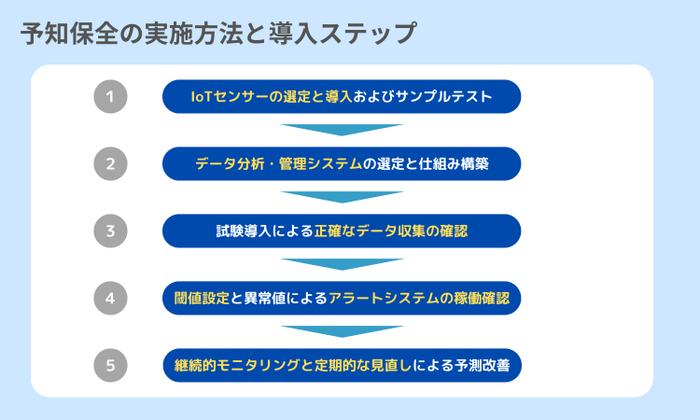
予知保全を導入するためには、具体的なステップに沿った計画的なアプローチが求められます。以下では、導入に必要な各ステップを詳しく解説します。
IoTデバイスとセンサーの選定・設置およびサンプルテスト
まず、予知保全を効果的に導入するためには、温度、振動、音、電流などのリアルタイムモニタリングに適したIoTセンサーを選定することが重要です。これにより、設備の異常を迅速に検知し、AIを活用したビッグデータ分析による精度の高い予測が可能となります。
ゼロからのスタートの場合、メーカーの専門家にアドバイスを求め、適した機器を選びます。選んだ機器は、リスクを減らすためにもレンタルしてサンプルテストを実施することが望ましいです。
センサーを設備に設置し、実際の稼働中に必要なデータが正確に収集できるかどうかを確認する作業は重要です。さらに、この段階では専任の保全担当者だけでなく、現場で実際に機器を扱うスタッフとともに機器の操作方法を習得することも推奨されます。
システム選定とデータ管理方法の確立
サンプルテストで必要なデータが確保できることが把握できたら、そのデータを効果的に活用するためのシステムを選定する段階に進みます。
適切なデータ分析ツールやクラウドベースの管理システムを選び、データの収集、保存、分析の仕組みを構築します。システム導入の前には、現場の運用に適しているかを確認し、管理方法の最適化を図る必要があります。
試験導入とデータ収集・分析
次に、選定したシステムを稼働させ、初期データの収集を開始します。
この段階では、通常時の稼働データと異常時のデータの両方を集め、設備の正常と異常のパターンを理解することが目標です。データ収集の過程では、センサーの位置や設定を適宜調整し、正確なデータが取得できるように細かく確認します。
閾値設定とアラートシステムの導入
収集したデータをもとに、設備の異常を予測するための閾値を設定します。
この設定によって、メンテナンスが必要なタイミングを明確に判断できるようになります。設定された閾値を超えた場合には、アラートが自動的に発生するようシステムに組み込み、異常が検知された際には迅速に担当者へ通知されるように調整します。
継続的なモニタリングと改善サイクルの構築
システムの導入後も、設備の状態は変化し続けるため、データのモニタリングは継続して行われるべきです。
データの分析結果に基づき、必要に応じて閾値やセンサーの設定を見直し、AIや機械学習を活用して予測精度を向上させます。定期的にフィードバックを取り入れ、データを活用したメンテナンスの効果を評価しながら、さらなる改善を目指すことが重要です。
まとめ
予知保全の導入には、IoTセンサーの選定やシステム構築、データ収集と分析、そして異常を通知するアラート機能の設定など、計画的なステップが必要です。導入後は、継続的なモニタリングとフィードバックを通じて、予測精度を高め、保全体制を最適化することが重要です。このサイクルを繰り返すことで、設備の効率的な運用とコスト削減が実現します。
予知保全(PdM)とその他保全手法との比較
この章では、予知保全を他の主要な保全手法と比較し、それぞれの違いや特徴を明らかにします。各保全手法との違いを解説し、どのような状況でどの手法が最適かを示します。
予知保全(PdM)と事後保全(Breakdown Maintenance:BM)の違い
予知保全と事後保全は根本的に異なる保全アプローチを持っています。事後保全は、設備が故障した後にメンテナンスを行う「修理」型のアプローチです。故障が発生した後にのみ対応するため、突発的なトラブルに迅速に対処する必要があり、設備の稼働に依存する生産体制にリスクを抱える可能性があります。
一方で、予知保全はリアルタイムでのデータ収集と分析を活用し、故障の予兆を察知して予防的にメンテナンスを行う「防止」型のアプローチです。これにより、ダウンタイムを最小限に抑えることが可能であり、設備の寿命を延ばすことが期待できます。BMは初期投資が低い反面、突発的な対応が必要となるため、長期的にはコストが増加するリスクがあります。
予知保全(PdM)と時間基準保全(Time Based Maintenance:TBM)の違い
予防保全の一つであるTBMは、一定の期間ごとに決まったメンテナンスを実施する、いわゆる「定期保全」のアプローチです。
たとえば、3ヶ月ごとの定期点検や1年ごとの部品交換など、時間を基準としてメンテナンス計画を立てます。この手法は、生産計画に反映しやすく、メンテナンスのタイミングが事前に決まっているため、スケジュール管理が容易です。しかし、実際にはまだ故障の兆候が見られない部品を交換することが多く、「突発的なトラブル」に弱く、「オーバーメンテナンス」になりやすいというデメリットがあります。
一方で、予知保全はリアルタイムで設備の状態を監視し、AIや機械学習を活用して故障の兆候を予測することで、必要なタイミングでのみメンテナンスを実施する手法です。予知保全では、過去のデータや運用履歴を基に予測モデルを作成し、最適なタイミングで部品交換や点検を行うことができるため、無駄なメンテナンスを減らしつつ、設備の稼働率を最大限に高めることが可能です。
予知保全(PdM)と状態基準保全(Condition Based Maintenance:CBM)の違いと類似点
予知保全とCBMは、基本的に同義の保全手法とされていますが、アプローチや技術に若干の違いがあります。日本産業規格(JIS)では、予知保全とCBMは同じカテゴリーとして扱われ、「状態基準保全」や「予兆保全」という呼び方も広く使用されています。これらの用語は、設備の状態に基づいて適切なメンテナンスを実施する点で共通しています。
ただし、予知保全とCBMの主な違いは、そのデータの利用方法と技術的なアプローチにあります。CBMは設備の状態をモニタリングし、設定した閾値に基づいてメンテナンスを実施する反応的な手法です。たとえば、振動や温度の上昇など、一定の異常が現れた時点でメンテナンスを行うというスタイルです。
一方で、予知保全はリアルタイムのデータ収集に加え、AIや機械学習を活用して未来の異常や故障の兆候を予測する、より「予測的」なアプローチを取ります。予知保全では、過去の故障データや運用データをもとに予測モデルを構築し、異常が発生する可能性が高まるタイミングを事前に察知することが可能です。この違いにより、予知保全はCBMよりも早い段階での対応が可能となり、設備の稼働率をさらに向上させることができます。
両者は「過剰なメンテナンスを避け、必要なときにのみ対応する」という予防的アプローチでは共通しています。しかし、予知保全は故障の兆候を「未来の予測」に基づいて捉えるため、AI技術の導入や高度なデータ分析が求められるのに対し、CBMは「現在の状態」に基づいて即座に判断を行うため、よりシンプルなデータ収集で運用可能です。
まとめ
予知保全はリアルタイムのデータ分析やAIを活用し、故障の予兆を予測する先進的な保全手法です。事後保全やTBMと比較して、ダウンタイム削減や効率的なメンテナンスが可能です。またCBMと類似点を持つ一方で、AIによる「未来予測」を特徴とし、より高度なメンテナンス計画を実現します。設備の状況に応じて最適な手法を選択することが重要です。
予知保全(PdM)導入の成功事例
企業が直面するさまざまな課題を、予知保全はどのように解決できるのか。この章では、3つの具体的な導入事例を紹介します。
化学製品製造会社A社:スマートバルブによるダウンタイム削減とコスト最適化
A社では、プラント内に4,000から5,000のバルブを設置しており、従来はこれらを年1回定期点検していました。しかし、定期点検の際にダウンタイムが発生し、その影響で保全コスト全体の20%を占める作業コストが課題でした。
そこでセンサー内蔵型のバルブとシステムを導入し、スマートバルブとして運用を開始しました。これにより、設備を停止せずにバルブの状態を診断できるようになり、ダウンタイムがほぼゼロに。さらに、保全コストも10%削減に成功しました。
冷凍機製造業B社:AI分析による異常予兆検知でのコスト削減
冷凍機の故障は、貯蔵中の食品の品質に深刻な影響を及ぼし、大きな損失につながります。B社では、トラブル防止のために頻繁に部品交換を行っていましたが、それに伴うコストと作業負担が問題となっていました。
そこで冷凍機にIoTセンサーを設置し、データ収集とAIによる分析を実施。異常や故障の予兆を早期に検知することで、必要な場合のみ部品を交換する運用に切り替えました。この結果、コストと負担が軽減され、顧客満足度も向上しました。
洗浄装置メーカーC社:フィルター管理の自動化による保全コスト削減
C社では、洗浄装置のフィルター交換をメーカーの推奨サイクルに従い、2ヶ月に1回フィルター交換を行い、月に1度は機械全体のメンテナンスを実施していました。しかし、その頻度の高さが保全コストの増加を引き起こしていました。
そこで流量計にセンサーを取り付け、洗浄液の循環流量を監視するシステムを導入しました。このシステムにより、フィルターの詰まりをリアルタイムで検知できるようになり、流量が低下した時のみ交換を実施。これにより、メンテナンス頻度を最適化し、労力とコストを大幅に削減することが可能になりました。
まとめ
予知保全の導入により、企業はさまざまな課題を解決しています。化学製品製造会社ではスマートバルブの活用でダウンタイムをほぼゼロにし、保全コストを10%削減。冷凍機製造業ではAI分析で異常を予測し、部品交換の頻度を最適化してコストと負担を軽減。洗浄装置メーカーではセンサーを活用したフィルター管理によって保全頻度を削減し、労力とコストの大幅削減を実現しました。
予知保全(PdM)導入時の注意点と課題
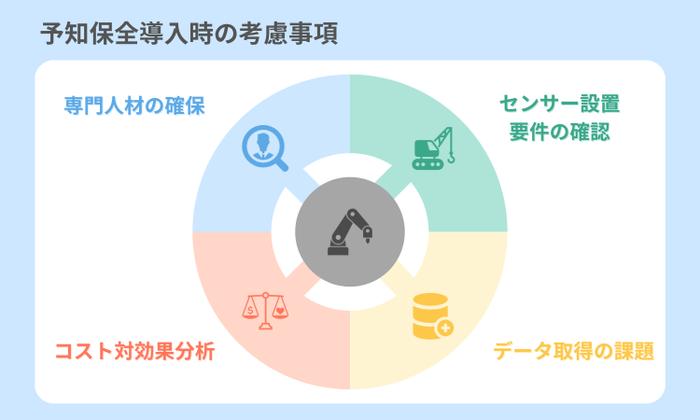
予知保全は多くの課題を解決する有効な手法ですが、万能ではありません。適切に機能させるためには、導入前に以下の点を十分に検討する必要があります。
センサーの設置が可能かどうかを確認する
予知保全の導入には、設備にセンサーを正確に取り付けることが不可欠です。もし、適切な場所にセンサーを設置できなければ、予知保全の効果は期待できません。
また、電源が確保できない、無線通信が届かない、WiFiの接続が安定しないといった状況では、センサーの稼働やデータ収集に支障をきたします。これらの要件を満たしているか、事前に確認することが重要です。
データの取得と閾値設定が可能かどうかを調査する
予知保全は正確なデータの収集が前提です。たとえばモーターの異音を検知しようとしても、工場内の騒音が測定の妨げになる場合があります。
同様に、プレス板のズレを振動で検知しようとしても、プレス機自体の振動が影響を与えることがあります。必要なデータを正しく取得できない場合、予知保全の効果は得られません。そのような場合は、別の保全手法の導入を検討するべきです。
コスト対効果の検討
予知保全を導入する際は、初期投資と運用コストが解決すべき課題に見合っているかを慎重に検討する必要があります。初期費用は高額になることが多いですが、長期的には人件費や部品交換費の削減につながる可能性があります。投資がどれだけの利益を生むかを評価するために、ROI(投資利益率)の算出が重要です。
導入にかかる初期費用とランニングコストを正確に見積もり、ダウンタイムの減少やメンテナンス費用の削減といった予想される利益を数値で比較・分析することが求められます。
データ分析を担える人材の確保と育成の必要性
予知保全を成功させるには、システム構築や大量のデータ分析、AIによる予測モデルの作成といった専門的なスキルが不可欠です。これらの技術を扱えるスタッフが社内にいない場合、システムの運用や管理は難しくなります。
さらに、AIやIoT技術は急速に進化しているため、最新の知識を常に追いかける必要があります。専任のスタッフを社内で育成することが理想ですが、難しい場合は外部の専門家を招くことも選択肢の一つです。いずれにせよ、予知保全の導入を検討する際には、必要なスキルを持つ人材が社内にいるかどうか、あるいはそのような人材を育成するためのリソースが確保できるかを慎重に見極めることが重要です。
まとめ
予知保全の導入には、センサー設置の可否や正確なデータ収集の環境整備、初期投資に対するコスト対効果の検討が重要です。また、データ分析やAI活用に必要な専門人材の確保・育成が成功の鍵となります。これらの課題を事前に確認し、適切な計画を立てることで、予知保全の効果を最大限に引き出すことが可能です。
予知保全(PdM)で設備の信頼性を高め、運用効率を最大化しよう
予知保全はIoTセンサーやAI技術を活用し、設備や機械の状態をリアルタイムで監視・予測する保全手法です。故障の予兆を事前に察知し、最適なメンテナンスを計画することで、設備のダウンタイムを削減し、生産性の向上やコストの最適化を実現します。
予知保全実践のポイント
- IoTセンサーやAIを活用した設備監視:リアルタイムでのデータ収集とAI分析により、故障予兆を早期に察知
- データ駆動型のメンテナンス計画:過去の運用履歴やデータをもとに最適な保全タイミングを決定
- 属人化の解消:AI技術により、経験や勘に頼らず高精度な判断が可能
- 継続的なモニタリングと改善サイクル:データ分析を基に設定を調整し、予知精度を向上
予知保全は設備の信頼性を向上させるとともに、企業のコスト削減や資産効率の改善を可能にします。一方で、初期導入コストや専門知識の必要性といった課題もあるため、事前の計画とスキルの整備が重要です。設備の長期的な最適運用を目指す企業にとって、予知保全は大きな価値を提供する手法になるでしょう。