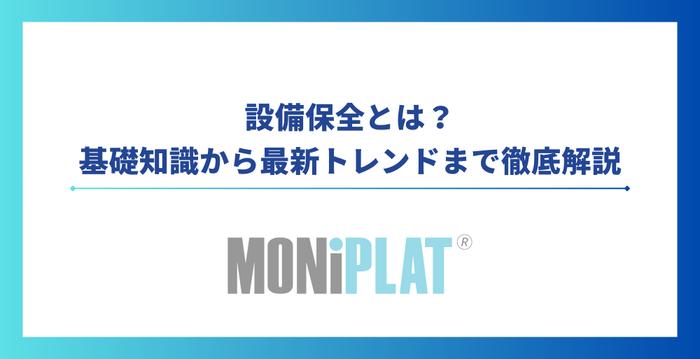
【2025年最新】設備保全とは?基礎知識から最新トレンドまで徹底解説
現代の製造業では、多種多様な設備が常に稼働しており、その安定した運用が生産活動の継続に欠かせません。この安定性を保つために重要なのが「設備保全」です。
設備保全とは、設備を最適な状態に維持し、予防的なメンテナンスを行うことを指します。設備保全は、単なる修理やメンテナンスにとどまらず、労働環境の改善や生産効率の向上にも直結します。また、少子高齢化や働き方改革といった社会的課題の解決にも大きく寄与します。
本記事では、設備保全の基本的な概念から具体的な保全方法、最新技術の導入事例までを幅広く紹介します。
設備保全とは?基本概念と目的
設備保全は機械製造の歩みとともにありました。そのため、長い歴史の中で、さまざまなコンセプトが生まれ、多種多様なアプローチが試みられています。現在のところ、設備保全は以下のように考えられています。
設備保全の定義
JIS(日本産業規格)は、設備保全を以下のとおり定義しています。
設備性能を維持するために、設備の劣化防止、劣化測定及び劣化回復の諸機能を担う、日常的又は定期的な計画、点検、検査、調整、整備、修理、取替えなどの諸活動の総称。
出典:[ JIS(日本産業規格) / 2021生産管理用語 ]
設備保全の目的と重要性
設備保全には、大きく分けて2つの主要な活動があります。
- 維持活動
- 改善活動
1つ目は、設備の正常な運転状態を保つための定期的な点検やメンテナンスを指す「維持活動」です。故障の予防や劣化の抑制が可能となり、稼働率を高く保つことができます。
2つ目は、現状の設備をさらに効率化・最適化するための改修や改善を目的とした「改善活動」です。生産性向上やエネルギー効率の改善を図るために、新しい技術を導入したり、プロセスを見直すことが行われます。
このように、設備保全は単なる修理だけでなく、持続的な設備の性能向上を目指す重要な業務です。
設備保全の主な目的とその重要性は、次の3点が特に重要です。
- 生産活動を維持する
- 不要なコストを削減する
- 安全性を確保する
1つ目は、設備及び設備内の部品を適切にメンテナンスすることで、異常や事故発生の可能性を軽減し、計画どおりの生産を維持することです。
2つ目は、整備不良により、品質の低下や不良品を生み出さないようにし、そのようなトラブルに対処することで人件費や保全工数が増えないようにします。
3つ目は、製造の現場で働く人々の命や健康を損なうような重大な事故が起きないように安全性の確保を徹底することです。
まとめ
設備保全は、設備を正常な状態に保つ「維持活動」と、設備の性能をさらに向上させる「改善活動」から成り立っています。これにより、生産活動の安定やコスト削減、安全性の確保などの目的が達成され、設備の持続的な運用が可能となります。
設備管理や保守・メンテナンス、修理との違い
設備保全に関連する活動には、設備管理や保守・メンテナンス、修理など、似たような用語が多く存在します。これらの違いを正しく理解することは、保全活動の目的を達成するために重要です。この章では、それぞれの用語の定義や役割について説明し、設備保全との違いを明確にします。
設備管理との違い
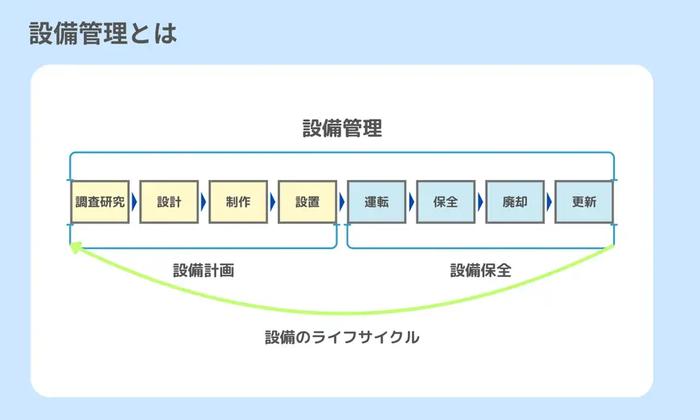
JIS(日本産業規格)によると、設備管理は次のように定義されています。
設備の計画、設計、製作、調達から運用、保全をへて廃却・再利用に至るまで、設備を効率的に活用するための管理。計画には、投資、開発・設計、配置、更新・補充についての検討、調達仕様の決定などが含まれている。
設備管理は、設備のライフサイクル全体にわたる広範な管理を指します。その中には、設備の設計や導入、運用、保全、廃棄といった工程が含まれています。この定義から、設備保全は設備管理の一部であることがわかります。設備管理は、全体的なプロセスの管理を重視しており、その一環として設備保全が行われるのです。
出典:[ JIS(日本産業規格) / 2021生産管理用語 ]
保守・メンテナンスとの違い
保守・メンテナンスは「設備に異常や故障が生じないように見守り、必要に応じて整備や修理を行うこと」であり、一般的には設備保全とほぼ同種の活動と解釈されています。
設備を提供している企業が顧客に対して行うサービス活動を「保守・メンテナンス」、設備を使用している企業が自らの設備を主体的に維持する活動を「設備保全」と使い分ける場合もあるようです。
修理との違い
JIS(日本産業規格)は、修理をこのように定義しています。
故障による停止、または有害な性能低下をきたしている設備に対し、正常・良好な状態を回復させる活動全般。
故障している設備を正常・良好な状態に回復させるために行う工事を「修理工事」と言い、緊急修理工事・時後修理工事・予防修理工事・定期修理工事などがある。
故障に至った真の原因をつかみ、再発防止を完壁に織り込んで設備を正常・良好な状態に回復させる「完全修理」、機能停止または有害な性能低下をきたすほどの故障に至らず、正常・良好な状態から外れている設備を元の状態に回復させる「小修理」がある。
設備保全は、設備が順調に稼働を続けられるようにするためのトータルな活動であり、修理は設備にトラブルが起きた際に行う処置です。ゆえに、修理は設備保全の一部であると言えます。
出典:[ JIS(日本産業規格) / 2021生産管理用語 ]
まとめ
設備保全に関連する「設備管理」「保守・メンテナンス」「修理」は、それぞれ異なる役割を持っています。設備管理は設備のライフサイクル全体を管理する広範な活動で、設備保全はその一部です。保守・メンテナンスは、設備の正常運用を維持するための活動であり、修理は故障時に行う回復措置として、設備保全の一環に位置づけられます。
設備保全における現代の課題
現代の製造現場では、設備保全に関連するさまざまな課題が存在しています。製造業のデジタル化や人手不足などの影響により、従来の保全方式だけでは対応が難しいケースが増えています。ここでは、設備保全における代表的な課題とその背景について解説します。
設備の老朽化
多くの製造業の設備は長年にわたって稼働し続け、老朽化が進行しています。特に高度成長期に導入された設備が多くの現場で依然として使用されており、これらの設備が適切なメンテナンスを受けないまま稼働し続けることで、故障や事故のリスクが高まっています。
設備の老朽化による故障は、突発的な生産停止や重大な事故につながる可能性があるため、計画的な更新や改修が不可欠です。
対応としては以下が挙げられます。
- 定期的な点検とメンテナンスを徹底し、設備の寿命を正確に把握する
- 設備更新や改修のタイミングを計画的に検討し、必要な投資を行う
人手不足と技術継承の課題
設備保全においては、熟練技術者の引退とともに、技術継承の問題が深刻化しています。特に、製造業全体で進行する少子高齢化の影響を受け、若手技術者の確保が難しくなっています。加えて、保全業務が特定のベテラン技術者に依存する傾向があり、業務の属人化が進んでいる現場も少なくありません。
これにより、技術継承がうまく進まず、保全の質が低下するリスクが高まっています。
対応としては以下が挙げられます。
- 若手技術者の育成プログラムを強化し、ベテラン技術者からの技術伝承を計画的に進める
- デジタル技術を活用し、技術的なノウハウをデータベース化することで、属人化を防ぐ
資金や人材不足による適切な維持管理の遅延
設備保全に必要なリソース(資金や人材)の不足が原因で、適切なメンテナンスが後回しにされることも増えています。
特に中小企業では、メンテナンス費用を確保できない場合があり、その結果、設備の状態が悪化し事故や故障が発生しやすくなります。設備のダウンタイムが増えることで、結果的に企業の生産性や信頼性に悪影響を与えるリスクがあります。
対応としては以下が挙げられます。
- メンテナンスコストの見直しを行い、コスト効率の高い保全手法を導入する
- 政府や業界団体からの助成金や補助金を活用し、保全資金を確保する
まとめ
現代の設備保全では、老朽化、人手不足と技術継承、資金や人材不足が大きな課題となっています。これらの問題は、設備の維持やメンテナンスの遅延を招き、生産性や安全性に影響を与える可能性があります。定期的なメンテナンス計画やデジタル技術の活用、資金支援の確保などが解決策として重要です。
設備保全の種類と進化:5つの方式を徹底解説
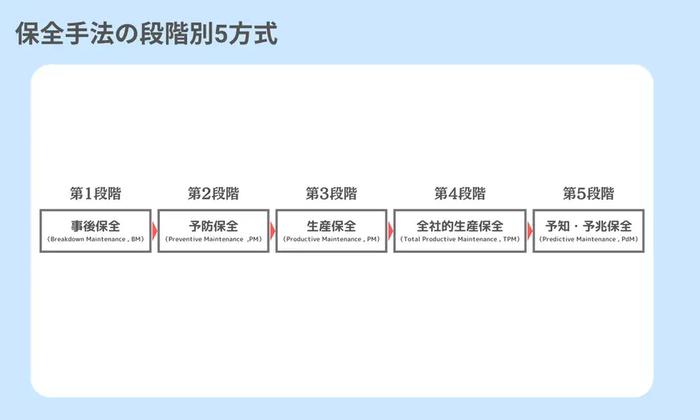
設備保全は、工場や製造現場において生産設備の稼働率を維持し、故障を未然に防ぐための重要な活動です。設備の進化とともに、保全方式も段階的に進化してきました。この章では、保全の種類を5つの方式に分類し、それぞれの特徴と進化について詳しく解説します。
第1段階:事後保全(Breakdown Maintenance:BM)
事後保全は、設備や機械に故障や不具合が発生した後に対応する保全方式です。設備の異常が発生した際に修理や部品交換を行うため、初期投資や保守費用が低く抑えられる一方、計画外の設備停止や重大な故障につながるリスクがあります。
特徴としては以下が挙げられます。
- 設備が停止してから対応するため、日常的なメンテナンスは不要
- 初期コストは低いが、突然の故障による生産停止や高額な修理費用が発生するリスクが高い
- 小規模事業者や資金が限られている企業にとっては有効な選択肢となることがある
- 突発的なトラブル対応が頻発することで、作業員の心理的負担が増加し、ストレスや疲労が蓄積されやすい
社会課題としては以下が挙げられます。
- 予算が限られている中小企業や工場で、メンテナンス費用が確保できない問題に対応
- ただし、突発的な故障による生産停止が、顧客への納期遅れや売上減少を引き起こす可能性がある
- また、突発対応が作業員の心理的負担を増加させ、ストレスや疲労が蓄積する問題もある
対応としては以下が挙げられます。
- 急な設備停止が許容できる場合には有効な手段
- ただし、作業員の心理的負担軽減や働き方改革を推進するためには、長期的には計画的な保全が望ましい
第2段階:予防保全(Preventive Maintenance:PM)
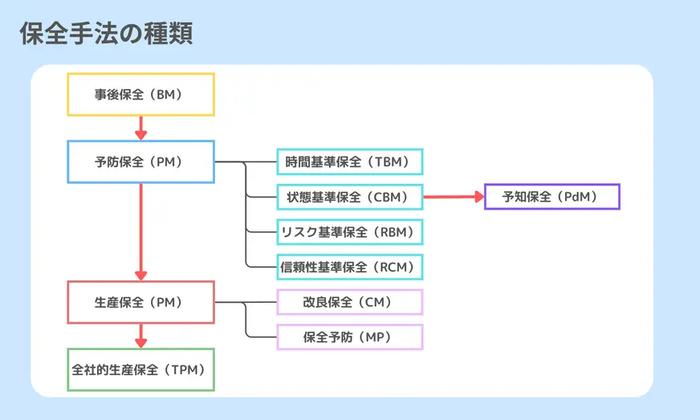
予防保全は、設備が故障する前に計画的に保守を行う方式です。設備の寿命を予測し、定期的なメンテナンスを実施することで、設備の故障リスクを減らし、生産効率を向上させます。
特徴としては以下が挙げられます。
- 設備の稼働時間や寿命に基づき計画的なメンテナンスを実施
- 突発的な故障を予防し、計画外のダウンタイムを削減できる
- 過剰なメンテナンスが発生する場合もあるため、設備の状態に基づく適切な管理が重要
社会課題としては以下が挙げられます。
- 生産ラインの停止や設備の故障が、供給チェーン全体に悪影響を与えるリスク
- 過剰なメンテナンスによるリソース浪費が問題
対応としては以下が挙げられます。
- 予防保全により、突発的な故障や生産停止を回避できる
- リアルタイムの設備状態監視を導入することで、必要最小限のメンテナンスが可能
予防保全には、以下の4つの具体的な方法があります。
時間基準保全(Time-Based Maintenance:TBM)
あらかじめ決められた運転時間や期間に基づいて、定期的にメンテナンスを行う方法です。一定期間で保守するため、過剰なメンテナンス(オーバーメンテナンス)が発生する可能性もありますが、故障による生産ロスを抑えるメリットがあります。
特徴としては以下が挙げられます。
- 設備の運転時間や稼働日数に基づいて定期的にメンテナンスを行う
- 故障のリスクは減少するが、実際の劣化状態に応じないため無駄なメンテナンスも発生する可能性がある
- 突発的な故障やトラブルが発生するリスクがあり、計画外の対応によって予想外のダウンタイムや追加コストが発生する可能性もある
状態基準保全(Condition-Based Maintenance:CBM)
設備の運転状態や部品の摩耗度などを監視し、設備の状態に応じてメンテナンスを行う方式です。CBMでは、設備の状況に基づいて保守のタイミングを決めるため、効率的なメンテナンスが可能です。これにより、無駄なメンテナンスを省き、コストを削減できます。
特徴としては以下が挙げられます。
- 設備の状態や劣化具合に応じて、必要なタイミングでメンテナンスを実施
- 状態監視が必須で、適切にメンテナンスを行うことでコスト削減と設備寿命の延長が可能
リスク基準保全(Risk-Based Maintenance:RBM)
設備の故障が引き起こすリスクを評価し、リスクの高い箇所に重点を置いて保守を行う方式です。特に重要な設備や、故障によって大きな影響が出る部分を優先してメンテナンスを実施します。
特徴としては以下が挙げられます。
- 故障リスクを評価し、重要度の高い設備に重点的にメンテナンスを行う
- リスク管理を重視するため、重大な事故や停止を回避できる
信頼性中心保全(Reliability-Centered Maintenance:RCM)
設備の重要度や故障の影響を分析し、各設備に最適な保全方法を選定する方式です。RCMは、コストとリスクのバランスを取りながら、保全戦略を策定するアプローチで、特に複雑な設備や大規模なシステムに有効です。
特徴としては以下が挙げられます。
- 設備の重要度に応じて、最適なメンテナンス方法を選定する
- コストと信頼性のバランスを取りつつ、効率的な保全戦略を構築する
第3段階:生産保全(Productive Maintenance:PM)
生産保全は、設備の生産性を最大化することを目的とした保全方式です。生産設備の稼働率を向上させながら、保全にかかるコストを最小化することを目指します。
特徴としては以下が挙げられます。
- 生産性を維持しつつ、設備の故障リスクを最小化する
- 設備の改良や保全予防により、設備の稼働率を向上させる
- 設備投資に加え、メンテナンス体制の向上が求められる
社会課題としては以下が挙げられます。
- 労働力不足や設備の老朽化による生産効率の低下
- 設備の修理にかかる時間とコストの増加
対応としては以下が挙げられます。
- 改良保全や保全予防により、設備寿命を延ばし、メンテナンス回数を減らす
- 設備の改善により、労働効率を高め、少ないリソースで生産性を維持する
生産保全には以下のようなサブカテゴリーがあります。
改良保全(Corrective Maintenance:CM)
設備の故障や不具合が発生した際、その原因を根本的に解決するための改善を行う方式です。故障が再発しないよう、設備自体の改良や部品の材質変更などを行います。
特徴としては以下が挙げられます。
- 故障原因を根本的に改善し、同じ問題が再発しないようにする
- 設備の材質や設計の改善が含まれ、長期的にコスト削減と生産効率の向上を目指す
保全予防(Maintenance Prevention:MP)
設備の設計段階で故障のリスクを予測し、あらかじめ対策を講じることで、将来的な保全コストを削減する方式です。新たな設備の導入時に、メンテナンスの効率化を考慮して設計します。
特徴としては以下が挙げられます。
- 設計段階で故障リスクを予測し、対策を講じてメンテナンスの手間を減少
- 長期的に見て、設備のトラブル発生頻度を低減し、保守費用を削減する
第4段階:全社的生産保全(Total Productive Maintenance:TPM)
TPMは日本で生まれた独自の保全方式で、企業全体で保全活動を行い、全員参加型の改善活動を推進します。
JIS(日本産業規格)は以下のように定義しています。
- 生産システム効率化の極限追求(総合的効率化)をする企業の体質づくりを目標とする
- 生産システムのライフサイクルを対象とし、“災害ゼロ・不良ゼロ・故障ゼロ”などあらゆるロスを未然防止する仕組みを現場現物で構築する
- 生産部門をはじめ、開発、営業、管理などの全部門で臨む
- トップから第一線従業員に至るまで全員が参加する
- 重複小集団活動によって、ロス・ゼロを達成を目指す
TPMの目的は、設備の故障をゼロにすることだけでなく、企業全体の生産性と効率を最大限に高めることです。以下のような要素がTPMの実践において重要です。
5S | 内容 |
---|---|
整理 | 必要なものと不要なものを分け、不要なものを捨てる。 |
整頓 | 必要なものを使いやすい場に置き、誰もが分かりやすいように明示する。 |
清掃 | 常に清掃を行う。清掃は点検のはじまり |
清潔 | 誰もが、けがや病気をしないように衛生を保つ。 |
躾 | 決めたこと(ルールや順番)を全員で守るように習慣付けする |
6つのロス | 解説 |
---|---|
突発事故ロス | 効率化を阻害する最大の要因は、突発事故による故障停止ロスである。 |
段取り・調整ロス | 段取り中のロスと、試し加工によるロスを減らし、良品の生産を目指す。 |
立ち上がり・歩留まりロス | 立ち上がりのロスの最小化には、熱変化などの実態を測り、自動補正を行う。 |
工程不要ロス | 不良品の廃棄と手直しのためのロスには、生産保全の考えの取り入れが有効。 |
速度低下ロス | 基準スピードを上げて原因を把握するか、現場のサイクル線図を分析する。 |
空転・チョコ停ロス | 一時的なトラブルによるロス。現象をよく見て微欠陥を是正する。 |
TPMは従業員全員が参加し、組織全体で保全活動を行うことにより、設備の稼働率や安全性を向上させます。また、継続的な改善活動により、個人依存の少ない体制を構築し、技術の継承や効率化を図ります。
社会課題としては以下が挙げられます。
- 組織全体で設備の管理が分散し、効率的なメンテナンスが行えない
- 知識の共有不足により、技術者のスキルに依存するメンテナンス体制
対応としては以下が挙げられます。
- 全社的な取り組みにより、設備管理を組織的に行い、技術の継承や作業の効率化を図る
- 5S活動を通じて現場環境を改善し、事故やトラブルを未然に防ぐ
出典:[ JIS(日本産業規格) / 2021生産管理用語 ]
第5段階:予知保全・予兆保全(Predictive Maintenance:PdM)
予知保全は、AIやIoT技術を駆使して設備の状態をリアルタイムで監視し、故障の兆候を「予測」することでメンテナンスを行う最新の手法です。CBMが設備の「現在の状態」に基づくのに対し、PdMはデータ分析を通じて将来の故障を予測し、より計画的かつ効率的にメンテナンスを実施します。
特徴としては以下が挙げられます。
- AIやIoTによるビッグデータ解析を用いて、設備の異常を早期に「予測」し、故障を事前に回避できる
- CBMと異なり、データを基に将来の故障リスクを精緻に把握することで、突発的なダウンタイムを最小化する
- 最新技術の活用により、メンテナンスの精度が向上し、長期的なコスト削減と設備の寿命延長が可能
社会課題としては以下が挙げられます。
- 設備のダウンタイムが生産に大きな影響を与え、突発的な故障が多発する場合、従来のメンテナンス手法ではリスクを完全に排除できない
- 故障発生時の生産停止が長引き、計画的なメンテナンスが困難
対応としては以下が挙げられます。
- AIやIoT技術を活用して設備の状態をリアルタイムで監視し、故障の兆候を事前に察知することで、突発的な故障を回避し、ダウンタイムを最小限に抑える
- 将来の故障リスクをデータ分析で予測し、計画的に修理を実施することで、予期せぬ生産停止を防ぐ
まとめ
設備保全の方式は、設備の進化に合わせて5つの段階に発展してきました。第1段階の「事後保全」から第5段階の「予知保全」に至るまで、それぞれ異なる特徴と利点があり、段階的に予防性や効率が高まります。最新の予知保全はAIやIoT技術を活用し、設備のダウンタイムを最小化するための手法です。
業務内容や必要な知識・スキル、役立つ資格
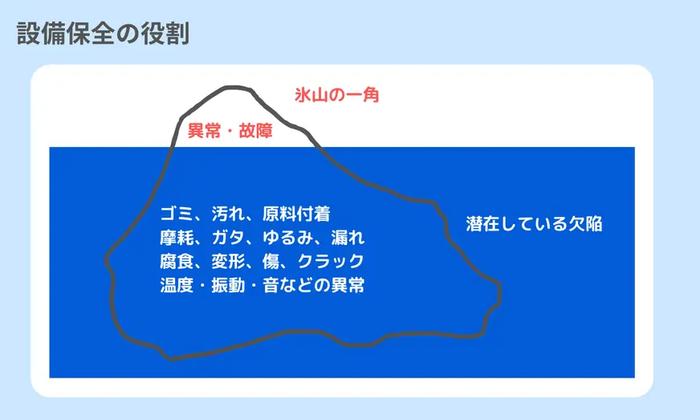
現在の設備保全において、もっとも重要な概念は「未然防止」です。異常や故障はしばしば氷山の一角にすぎず、その背後には多くの潜在的な欠陥が隠れている可能性があります。
これらの問題を放置してしまうと、やがて異常や故障が表面化し、さまざまなロスや生産停止といった影響をもたらすことになります。設備保全の役割は、こうした潜在的な欠陥を「見える化」し、適切な対策を講じることで、異常や故障の発生を未然に防ぐことにあります。
設備保全の仕事内容
製造する製品や稼働環境によって内容は異なりますが、設備保全の基本的な役割を果たすために、以下のような業務が一般的に行われています。
設備の点検・監視
静止時・運動時両面の設備の状態をチェックして、整備の必要性を判断します。また、ポイントとなる数値や状態を記録し、部品交換や調整が必要な場合は処置します。
設備の定期的な整備
一定期間ごとに部品を交換するなどの整備を行います。その期間は、前述した保全の種類により異なります。
設備の不具合の修復
設備に異常や故障が発生した場合に修理を行います。軽度のものから複雑なものまで、修復の度合いも保全の種類により異なります。
設備保全に向いている人とは?必要なスキルや資格など
設備保全担当者に求められる最も重要な能力は、異常や故障の兆候を早期に察知し、トラブルを未然に防ぐことです。
そのためには、異常や故障を素早く発見できることに加え、正確かつ迅速に対処できる能力、正常と異常を定量的に判断する力、定められた基準を厳守する力が必要です。
さらに、生産の基本知識や改善方法、設備の構造と機能などに関する知識を積極的に身につけようと努め、自分が担当する設備をしっかり守ろうとする意識と責任感があれば適任まちがいありません。設備保全の能力を認める資格としては機械保全技能士や電気工事士、電気主任技術者、ビル設備管理技能士などがあります。
資格がなくてもできる設備保全業務は多くありますが、資格取得の際に学ぶ知識やスキルは、現場で非常に役立ちます。特に機械保全技能士は、メンテナンス方法や検査方法をはじめ、設備に関して幅広い知識を得ることができる資格なので、設備保全業務に就くことになった方は取得しておいたほうがよいでしょう。
まとめ
設備保全では、異常や故障を「未然防止」するための点検・整備・修理が重要です。担当者には、異常の早期発見や迅速な対処能力、基準の厳守が求められます。また、「機械保全技能士」などの資格が役立ち、現場で必要な知識とスキルを強化します。
設備保全の実施事例
設備保全の取り組みは、設備の規模、製品の種類、従業員の人数などによって異なります。ここでは、さまざまな業界における成功事例を紹介します。
製品出荷事業所:コンベア設備のトラブル解消と安定化
稼働年数40年を迎えた工場の事例です。工場内の搬送設備は、すべて事後対応に頼っていたため、トラブルによるライン停止が頻繁に発生していました。
さらに、設備のリスト化や重要度の把握が不十分で、全体的な保全計画を立てるのも困難な状況でした。保全担当者は、まず設備ごとの日常保全を計画し、実行方法を標準化して進めました。
その結果、ライン停止に直結する重大なトラブルが約4割減少し、突発的な故障も約3割減少しました。この成果を受け、社員全体の意識が向上し、工場全体で積極的に保全活動に取り組む姿勢が浸透しました。
プラスチック製品製造工場:新設工場の中長期保全計画の立案
新設されたプラスチック製品製造工場では、生産を安定させるための明確な指標や施策が必要とされました。保全担当者は、中長期的な保全計画を策定し、その計画を実行した結果、工場はトラブルなく順調に生産を開始することができました。
さらに、保全にかかる予算や設備稼働時間のベンチマークを設定し、経営戦略における管理指標を明確化しました。また、保全業務に従事する社員の作業負担が軽減されたため、結果として離職率の低下にも寄与したと評価されています。
無線型振動計を活用した設備監視システム
石油化学誘導品工場の事例です。従来の設備診断や日常点検は、保全担当者が五感を使った状態監視で行っていました。この方法では、異常の判断が担当者のスキルや経験に依存しやすく、他の人への引き継ぎが難しいという課題がありました。さらに、保全担当者にかかる業務負担の軽減も大きな問題でした。
そこで、この工場では、設備に稼働データを収集する無線型振動計を導入し、プロセスデータを活用するシステム基盤を整備しました。リアルタイムでのデータ監視によって異常の検知精度が大幅に向上し、遠隔監視の導入によって現場作業の負担も大きく軽減することができました。
神奈川県企業庁:モニタリングシステムによる発電所の遠隔監視
神奈川県企業庁が運営する水力発電所では、すでに遠隔監視システムが導入されていましたが、取得できる情報量が限られていたため、トラブルが発生した際に問題の原因を把握するには、現場に出向く必要がありました。
トラブル発生後、現場で詳細な状況を確認し、その後に原因を調査するため、対応に時間がかかり、復旧までに大幅な遅れが生じることが課題でした。この課題を解決するため、発電所では新たに高精細なカメラとセンサーを導入し、データの収集・格納・分析を行うシステムも新たに導入しました。
これにより、遠隔地からでも設備の状態を詳細に把握できるようになり、トラブルの原因を現場に行く前に推定し、迅速に対応策を立案することが可能となりました。
まとめ
設備保全の実施事例として、コンベア設備の安定化、プラスチック製品工場の中長期保全計画、無線型振動計による遠隔監視、発電所のモニタリングシステムなどが挙げられます。これらの事例から、適切な保全計画や監視システム導入が、トラブルの減少や業務負担の軽減に有効であることが示されています。
IoT・AI活用による設備保全の今後の展望と未来
設備の高度化や複雑化が進む中、設備保全にも新たな課題が次々と浮上しています。多くの業界で共通する問題ですが、特にこの分野における人材不足は、経営層にとって大きな悩みの種です。予知保全(予兆保全)においては、高度なスキルと豊富な経験が求められるため、必要な人材を確保し、その能力を十分に活用するのが難しくなっています。
こうした課題に対する解決策として、IoTやAIの活用が注目されています。これらの技術を導入することで、設備からリアルタイムにデータを収集し、遠隔地からでも状態の監視や制御が可能となります。この結果、保全業務がより効率化され、少人数でも運営できるようになり、業務負担の大幅な軽減が期待されています。
さらに、これらのテクノロジーは「守り」の保全にとどまらず、「攻め」の保全業務をも実現すると期待されています。特に、AIは設備から収集されたデータをもとに、異常や故障の早期察知や、最適な整備スケジュールのプランニングを行うことが可能です。
これにより、故障による生産停止のリスクが大幅に低減されるだけでなく、これまで予測不可能だったトラブルも事前に把握し、計画的なメンテナンスで設備の稼働率を最大化できると期待されています。こうした技術の導入は、設備保全のあり方そのものを革新し、新たな製造業の未来を切り拓く可能性を秘めています。
まとめ
設備保全の分野では、IoTやAIの導入が注目されており、これによりリアルタイムでのデータ収集や遠隔監視が可能になります。これらの技術は、保全業務の効率化や予知保全の実現に貢献し、設備のダウンタイムを減らし、計画的なメンテナンスを支援します。こうした革新により、製造業の未来が大きく変わることが期待されています。
設備保全の重要性を理解した上で、自社に最適な手法を導入して生産性&安全性アップ
設備保全は生産設備を安定した状態で稼働させ、故障を未然に防ぐための重要な活動です。歴史と共に進化してきた設備保全は、現在では多様な方式が存在し、保全業務の効率化や安全性の確保、生産性の向上に寄与しています。さらに、AIやIoTの技術を活用することで、保全業務の効率化や計画的なメンテナンスが可能となり、設備保全の未来が大きく変わろうとしています。
設備保全の実践におけるポイント
- 保全方式の選定:設備や現場のニーズに合った保全方式を選定し、段階的な実践を図る
- 効率的な技術継承:熟練技術者の知識をデジタル化してデータベース化し、属人化を防止
- 定期的な見直しと改善:保全計画の定期的な見直しと、必要に応じた改修・改善を継続的に実施
設備保全は単なるメンテナンス活動に留まらず、組織全体の生産性と安全性を高めるための戦略的な取り組みです。特に人材不足が深刻な現代の製造業において、IoTやAIを活用したCBMや予知保全の導入は、限られたリソースで効率的な保全体制を構築するうえで重要な役割を果たしています。
設備保全を効率的に管理するならMONiPLATがおすすめ
設備保全は、生産性の向上や設備の長寿命化に欠かせない重要な取り組みです。特に、予防保全におけるTBMやCBMを効果的に実施することで、故障リスクを減らし、安定した稼働を実現できます。
MONiPLATは設備保全業務を一元管理できるクラウドシステムとして、TBMやCBMの実践をサポートします。直感的なインターフェースにより、端末上で保全項目の確認、点検結果の記録、作業履歴の保存・分析が簡単に行えます。
設備保全の効率化と最適化をお考えの企業は、ぜひMONiPLATの導入を検討してみてください。