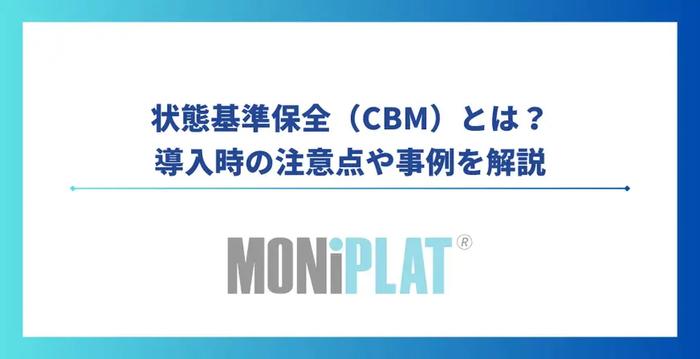
【2025年最新】状態基準保全(Condition Based Maintenance:CBM)とは?導入時の注意点や事例を解説
デジタル化の加速やグローバル競争の影響により、製造現場では設備の老朽化、コスト削減のプレッシャー、そして経験豊富な技術者の退職に伴う人材不足といった多くの課題に直面しています。
その中で状態基準保全(CBM)は、設備の状態に応じたメンテナンスを行い、最適なメンテナンス周期の確立や、予期せぬ故障を防ぐことで、ダウンタイムの削減やコスト削減、生産性向上を実現する革新的な手法として注目を集めています。
本記事では、CBMの基本概念、導入のメリット・デメリット、導入事例などを紹介し、企業が設備保全を最適化するための具体的なポイントを解説します。
状態基準保全(CBM)の基本概念
CBMを理解するには、その歴史や定義、特徴、そして現代の製造業で果たす役割を押さえることが重要です。以下でその全体像を見ていきましょう。
状態基準保全(CBM)の起源と歴史
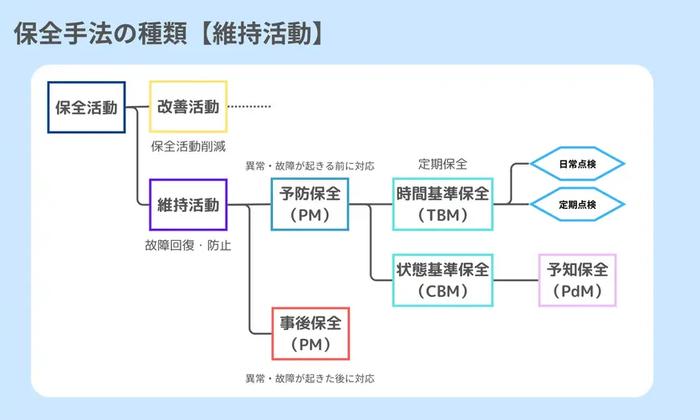
機械による生産が普及し始めた初期の頃、設備の保全は事後保全(Breakdown Maintenance:BM)が一般的でした。事後保全では設備が故障してから修理や交換を行うため、生産が頻繁に中断し、効率が低下するという課題がありました。
大量生産の時代に突入すると、予期せぬ設備故障による生産停止が企業にとって大きなリスクとなり、より効率的な保全方法が必要となりました。そこで1920年代のアメリカで提唱されたのが、異常を未然に防ぐ予防保全(Preventive Maintenance:PM)です。
予防保全は、定期的な点検・修理を行う時間基準保全(Time Based Maintenance:TBM)に発展しましたが、TBMでも設備が正常な場合でも過剰な部品交換が行われることがあり、余分なコストや生産停止が問題となりました。これらの課題を解決するため、設備の状態に基づいてメンテナンスを行うCBMが提唱されました。
状態基準保全(CBM)の定義と特徴
CBMは設備の状態をリアルタイムで監視し、異常や劣化が発生する前に適切なメンテナンスを行う手法です。たとえばセンサーを使用して、部品の摩耗度や温度、振動などの指標をモニタリングし、設定した閾値を超えた場合に自動的に警告が発せられ、適切な対策が講じられます。
CBMの最大の特徴は、突発的なトラブルの防止とメンテナンス周期の最適化です。正常な設備に対して不必要な修理や交換を行わず、問題が発生する前に対処できるため、コスト削減や設備稼働率の向上に貢献します。
ただし、設備の状態を正確に把握するためには、センサーやAIを活用した高度な技術が必要となる場合があります。
状態基準保全(CBM)の目的と重要性
CBMの主な目的は、無駄なメンテナンスを減らし、設備のダウンタイムを最小限に抑え、コスト削減を図ることです。これにより、生産活動の安定化や設備の寿命延長が実現されます。
近年、CBMが注目されるもう一つの背景には、現場における技術者不足や熟練従業員の退職問題があります。設備の老朽化が進む中で、IoTやAI技術を活用したCBMは、設備の状態をリアルタイムで把握し、予測メンテナンスを可能にします。
これにより、経験の浅い従業員でも効果的に設備を管理でき、製造現場全体の保全力向上につながります。
まとめ
CBMは設備の状態をリアルタイムで監視し、異常が発生する前に最適なメンテナンスを実施する手法です。従来の事後保全や時間基準保全の課題を解決する形で発展し、無駄な作業を削減しながら生産性向上やコスト削減を実現します。また、IoTやAI技術の活用により、技術者不足や設備老朽化といった現場課題への対応力も強化されています。
状態基準保全(CBM)のメリット・デメリット
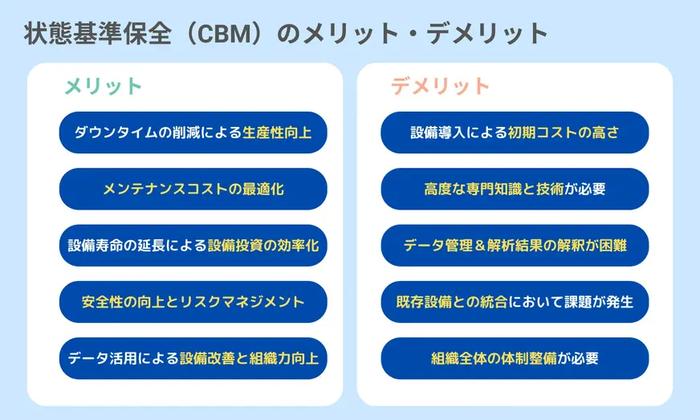
CBMは従来の保全方法にはない利点を持っていますが、一方で導入や運用における課題も存在します。この章では、CBMのメリットとデメリットを詳しく見ていきます。
状態基準保全(CBM)のメリット
CBMの導入には、さまざまな利点があります。代表的なメリットを以下の5つのカテゴリで解説します。
ダウンタイムの削減と生産性の向上
設備に故障や異常が発生すると、ダウンタイム[注1]が生じ、生産に大きな影響を与えます。CBMは、異常を未然に防ぎ、計画的なメンテナンスを実施することで、ダウンタイムを減らし生産性を向上させます。
- 予防的な対応:設備の状態をリアルタイムで監視し、異常の兆候を早期に検知。計画的なメンテナンスを行い、突発的な生産停止を防止
- 迅速な問題解決:異常箇所を正確に特定できるため、復旧作業が効率化され、停止時間を短縮
- 生産計画の安定化:ダウンタイムが減少することで、生産スケジュールの変更や納期遅延のリスクを低減し、顧客満足度を向上
- 設備の停止によって生産が中断する時間のこと
メンテナンスコストの最適化
CBMは設備の状態を元に必要なタイミングでのみメンテナンスを実施するため、コストの最適化に寄与します。
- 無駄な作業の削減:部品の早期交換や過剰な点検を避けることで、不要なメンテナンスコストを削減
- 資源の有効活用:人員や部品、工具などのリソースを効率的に配分でき、結果的にコスト削減が可能
- 在庫管理の改善:交換が必要な部品のタイミングを正確に予測できるため、在庫管理が容易になり、在庫過多や欠品を防止
- サステナビリティ:エネルギー消費の最適化を図ることで、環境負荷を低減し、長期的なコスト削減効果も
設備寿命の延長と投資効率の向上
設備の寿命を延ばすことは、設備投資の効率化に直結します。CBMは以下の点で設備寿命の延長に寄与します。
- 適切なメンテナンス:劣化の兆候を早期に発見し、適切なタイミングで部品交換や修理を行うことで、設備の状態を最適に保持
- 過負荷の防止:設備の異常や過負荷を早期に検知し、対策を講じることで、深刻な故障を防止
- 長期的なパフォーマンス維持:定期的な状態監視により、設備の性能劣化を防ぎ、長期間にわたって安定した稼働を実現
安全性の向上とリスクマネジメント
設備故障は生産性の低下だけでなく、安全面でも重大なリスクを伴います。CBMは以下のように安全性の向上に貢献します。
- リスクの早期発見:異常な振動や温度上昇などの兆候をいち早く検知し、重大事故を防止
- 従業員の安全確保:設備の不具合による作業員の怪我や健康被害のリスクを軽減
- 法規制の遵守:法的な安全基準や規制に対応したメンテナンスを実施し、コンプライアンスを確保
データ活用による継続的な改善と組織力の強化
CBMにより得られるデータを活用することで、設備の改善や組織力の向上に役立ちます。
- データドリブンな意思決定:収集されたデータを分析することで、設備の状態や保全活動の効果を客観的に評価し、より的確な経営判断が可能
- ノウハウの蓄積:設備の故障パターンや劣化傾向をデータとして蓄積し、今後の保全計画や新規設備の選定に活用可能
- 人材育成の促進:データ分析や最新技術の活用を通じて、従業員のスキルアップを図り、組織全体の技術力を向上
状態基準保全(CBM)のデメリット
CBMは非常に効果的な保全手法ですが、導入には以下のような課題も伴います。ここでは代表的なデメリットについて解説します。
初期導入コストの高さ
CBMの導入には、高度なセンサーやモニタリングシステムが必要で、これらの設備導入には大きな初期コストがかかります。注意すべきポイントは以下の通りです。
センサーおよび機器の導入コスト:各設備に取り付けるセンサーや機器の費用が高額になる可能性あり。リアルタイムでデータを収集するためのシステム構築にもコストが発生
システム統合コスト:既存の生産システムやERP(Enterprise Resource Planning)との連携が必要な場合、統合にかかるコストが増加する可能性あり
ランニングコストの発生:センサーやモニタリング機器の故障時には修理・交換費用が必要で、これらは長期的に発生するため、運用コストの継続管理が必要
専門知識と技術の必要性
CBMを効果的に運用するためには、設備保全やデータ分析に関する高度な専門知識が必要です。
- データ分析のスキル:センサーから収集したデータを適切に解析し、最適なメンテナンス時期を判断するためのデータ分析能力が必要。AIや機械学習を導入している場合、それらを活用する技術者も不可欠
- ソフトウェアの運用知識:モニタリングシステムやクラウドインフラを効率的に運用するためにはITスキルが必要。保全担当者がこれらを迅速に習得できない場合、外部の専門業者に依存するリスクあり
- センサーの適切な運用管理:センサーが正確に動作しなければ、信頼性の高いデータが得られない。センサーの定期的な校正やメンテナンスを行うためのスキルや、マニュアル整備が必要
データの管理と分析の難しさ
CBMはデータ収集とその分析に依存するため、データ管理の適切さが成功の鍵を握りますが、いくつかの難点があります。
- 膨大なデータの管理:多数の設備にセンサーを設置すると、大量のデータが生成され、このデータを効果的に保管・管理し、活用するためのインフラが必要。特に、クラウドを活用したデータベース設計やバックアップ体制の整備が必要
- 異常検知の精度向上:ノイズを減らし、異常や劣化の兆候を検出する技術は高度なものが求められる。AIや機械学習の導入においても、正確なデータセットが必要
- 解析結果の解釈の複雑さ:異常データが検出されても、直ちに重大な故障と結びつくわけではない。解析結果をどう解釈し、どのメンテナンスが優先されるべきか判断するには経験と直感が必要
既存設備との統合の難しさ
CBMを既存の設備に導入する際、技術的な統合や運用面での課題が生じます。
- レガシーシステムとの互換性:古い設備では最新のセンサーやシステムと互換性がないことが多く、改修や追加投資が必要となる場合がある。製造ライン全体をモニタリングする場合、既存システムとの統合が大きな課題となる
- 設備の物理的制約:センサーの設置場所やモニタリング範囲に制約がある設備では、全体をカバーできず、部分的にしかCBMを適用できない可能性あり
組織全体の体制整備が必要
CBMの導入は技術的な課題だけでなく、組織全体の体制にも影響します。
- 社内の文化・意識改革:従来の保全方法からCBMに移行するには、現場従業員が新しいシステムに慣れるまで時間がかかる。デジタル化への抵抗がある場合、従業員への教育とサポートが不可欠
- 部門間の連携強化:IT部門、保全部門、生産部門などが密に連携し、データやメンテナンスの優先度を共有しなければ、CBMの効果は最大化されず、部門間のコミュニケーションを強化することも重要
まとめ
CBMはダウンタイム削減やコスト最適化、設備寿命の延長、安全性向上など多くのメリットを提供します。しかし、導入時には初期コストや専門知識の必要性、データ管理の複雑さ、既存設備との統合、組織体制の整備といった課題があります。これらのメリットとデメリットを考慮しながら、適切な計画のもと導入を進めることが重要です。
状態基準保全(CBM)の実施方法と導入ステップ
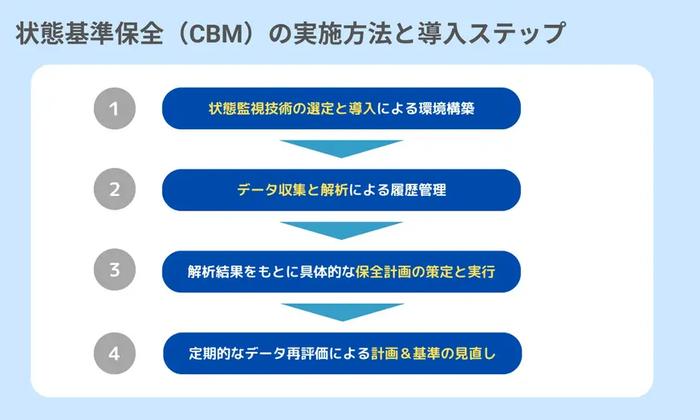
状態監視技術の選定と導入
まずは、どの設備や部品を監視するかを明確にします。特に、異常や故障が発生しやすい箇所や生産ラインの重要な箇所に重点を置くのが一般的です。次に、リアルタイムで設備の状態を把握できる指標を選定します。
- 温度:部品やシステムの過熱を防止
- 振動:機械の動作異常を検知
- 音:異常なノイズを検知
- 電流:電気設備やモーターの負荷を確認
- 油の劣化状態:潤滑油の品質を把握し、部品摩耗を防止
これらの指標を基に、適切なセンサーやモニタリングシステムを導入し、データ収集が可能な環境を整備します。
また、IoT技術を活用して遠隔から監視することで、運用の効率化が期待できます。
データ収集と解析方法
センサーによって収集されたデータは、CBMの核となる要素です。データはリアルタイムで一元管理され、長期的な傾向を分析するための履歴管理も重要です。
- リアルタイム性:設備の状態をリアルタイムで把握し、異常を即座に検知できること
- 履歴管理:長期的にデータを蓄積し、過去の傾向を分析して将来の予測に役立てること
AIや機械学習を用いてデータを解析することで、異常検知の精度が向上し、予防的なメンテナンスを最適なタイミングで行うことが可能です。手動監視では見逃されがちな微細な変化も、AIのパターン認識により早期にキャッチできます。
AI・IoTの発展によるCBMについての詳細は、以下の記事で解説しております。
保全計画の策定と実行
データ解析の結果を基に、メンテナンスの基準(設備の状態や実施内容)を設定し、具体的な保全計画を策定します。このステップで重要なのは、次の2点です。
- 優先順位の設定:データを基に、どの設備を優先的にメンテナンスするかを決定し、重要な設備やリスクの高い箇所を優先
- スケジュールの最適化:計画的なメンテナンススケジュールに従いながらも、設備の状態変化に応じて柔軟に対応
継続的な改善とフィードバック
保全計画を実行した後も、設備の状態は変化し続けます。定期的にデータを再評価し、保全計画や基準を見直すことが必要です。
- 改善策の導出:新たに収集したデータを元に、設備寿命の延長やコスト削減につながる改善策を探る
- フィードバック:現場へのフィードバックを行い、保全活動の質を高めることで、CBMの効果を最大化する
まとめ
CBMの導入には、段階的なアプローチが必要です。まずは監視対象や指標を選定し、センサーやIoT技術でデータ収集環境を整備します。その後、データを解析して保全計画を策定・実行し、設備の状態変化に応じて改善を重ねます。継続的なフィードバックを通じて、設備保全の精度と効率を向上させることが重要です。
状態基準保全(CBM)と他の保全手法との比較
CBMは他の保全手法と異なる特徴を持ちます。この章では、他の代表的な保全手法とCBMの違いを簡単に解説します。
時間基準保全(Time Based Maintenance:TBM)との違い
TBMは定期的なスケジュールに基づいて、設備や部品のオーバーホール[注1]や交換を行う手法です。予防保全の一種であり、事前にメンテナンスのスケジュールを立てやすい点が特徴です。
しかし、設備の状態に関係なくメンテナンスを行うため、正常な部品を交換してしまうことがあり、結果としてオーバーメンテナンスの可能性や突発的なトラブルに対応しきれないというデメリットがあります。
一方で、CBMは設備の状態に応じてメンテナンスを行うため、必要な時にのみ対応でき、無駄な作業を減らせるというメリットがあります。
CBMとTBMの違いについての詳細は、以下記事にて解説しております。
予知保全(Predictive Maintenance:PdM)との違い
予知保全はAIやIoTを活用して設備の状態をリアルタイムで監視し、故障の予兆を検知して適切な対応を行う保全手法です。CBMと予知保全は非常に近い手法ですが、予知保全はより予測に重点を置き、異常が発生する前に高度な分析を行って将来の問題を回避する点が特徴です。
CBMは現在の状態に基づいて判断するのに対し、予知保全は未来の故障リスクを予測する点で進んだ手法といえます。
事後保全(Breakdown Maintenance:BM)との違い
事後保全は設備が故障した後に修理や部品交換を行う保全方法です。CBMや他の予防保全手法とは異なり、故障が発生した後に対処するため、突発的なトラブルやダウンタイムが発生するリスクが高くなります。
その一方で、CBMは故障が起きる前に設備の状態を把握し、適切なタイミングでメンテナンスを行うため、突発的なトラブルを最小限に抑えることができます。
CBMと事後保全の違いについての詳細は、以下記事にて解説しております。
- ひとつひとつの部品にまで分解・点検し、必要とされる洗浄や修理などの処置を行うこと
まとめ
CBMは設備の状態に応じた効率的なメンテナンスを可能にする手法です。従来のTBMのような定期スケジュールに頼らず、無駄な作業を削減します。また予知保全と比較すると、CBMは現在の状態を重視する一方で、予知保全は将来のリスク予測に重点を置いています。事後保全との比較としては、CBMは故障発生前に対策を講じることでダウンタイムやトラブルを最小化する利点があります。
状態基準保全(CBM)導入の成功事例
多くの企業がCBMを導入して設備保全を効率化し、コスト削減や生産性向上を実現しています。この章では、3つの成功事例を紹介します。
また、以下記事でもCBMの導入事例について解説しておりますので、ぜひご確認ください。
鉄道会社A社:線路と車両の状態監視システムによる安全性と効率性の向上
A社では線路と車両にセンサーを設置し、リアルタイムでの状態監視を導入しました。特に、線路の歪みやレールの締結装置、ボルトの状態をカメラで自動撮影し、異常を検知します。撮影された画像データをもとに、電車走行時の影響を詳細に分析し、最適なタイミングでのメンテナンスが可能になりました。
これにより、安全性の向上と効率的なメンテナンスが実現し、無駄な作業の削減とコスト削減にも成功しています。
航空会社B社:エンジンコンディションの常時監視で飛行停止リスクを低減
B社では航空機のエンジンにセンサーを取り付け、温度や振動、圧力を常時監視するシステムを導入しました。
これにより、エンジンのコンディションを精密に把握し、異常が発生する前に適切なメンテナンスを実施できるようになりました。CBMの導入により、突発的な飛行停止リスクを大幅に減らし、航空機の寿命を延長することにも成功しています。
工作機器メーカーC社:ベアリングの状態監視で無駄な部品交換を削減
C社では、高速回転する自動旋盤機の主軸ベアリングの故障頻度が問題となっていました。従来は、事後保全で故障後に部品交換を行っていましたが、センサーを導入し、ベアリングの摩耗状態を常時監視することで状況を見える化しました。
データ解析を通じて、故障原因の早期特定や適切な部品交換のタイミングを判断するシステムを構築した結果、無駄な部品交換を削減し、コスト削減にも貢献できるようになりました。
まとめ
CBMの導入事例として、鉄道会社では線路と車両の監視で安全性と効率性を向上し、航空会社はエンジン監視で飛行停止リスクを低減、工作機器メーカーはベアリング監視で無駄な部品交換を削減しました。これらの事例から、CBMが多様な業界で安全性、効率性、コスト削減に貢献できることを伺えます。
状態基準保全(CBM)導入時の注意点と課題
CBMは多くのメリットをもたらしますが、導入にはいくつかの課題があります。この章では、CBM導入を決定する前に考慮すべき3つの重要なポイントを解説します。
初期コストの問題と回収方法
CBMは比較的新しい保全方法であるため、センサーやモニタリングシステムの導入に初期コストがかかります。これには、設備自体の費用だけでなく、設置や運用にかかる費用も含まれます。
無制限な投資は企業の経営を圧迫する可能性があるため、投資利益率(ROI)を明確にし、どれだけのコストが回収できるかを慎重に評価することが重要です。
データ品質と分析精度の向上
CBMの効果を最大限に引き出すには、データの質と分析能力が鍵となります。センサーやモニタリングシステムを設置しただけでは不十分で、収集したデータを正確に管理し、適切に分析することが重要です。
これにより、メンテナンスのタイミングや改善策を的確に判断できるようになります。保全業務においても、新製品開発と同様に、常により良い方法を探求する姿勢が求められます。
継続的な改善と教育
CBMの導入後も、継続的な改善と設備に合わせたメンテナンスの見直しが必要です。どれだけ優れた技術を導入しても、設備は必ず劣化し、製造環境や外部条件も変化します。また、センサーやモニタリング技術も進化し続けています。
そのため、導入後も定期的に保全計画を見直し、改善することが大切です。加えて、担当者の技術スキル向上のための教育活動も継続的に行う必要があります。
まとめ
CBMの導入には、初期コストの負担やROIの慎重な評価が求められます。また、データ品質や分析精度の向上が鍵となり、センサー設置だけでなく適切なデータ管理と分析が必要です。さらに、導入後も継続的な改善と担当者のスキル向上のための教育が不可欠なので、技術の進化に対応しながら計画を見直していくことが重要です。
状態基準保全(CBM)で設備の状態を最適化し、生産性とコスト効率を高めましょう
CBMは設備の状態をリアルタイムで監視し、異常や劣化の兆候を捉えることで、最適なタイミングでのメンテナンスを実現する手法です。従来の保全手法と比較して無駄を削減しつつ、ダウンタイムの低減や設備寿命の延長を目指すことができます。IoTやAI技術を活用したCBMは、設備保全の効率化と現場課題の解決に役立つ革新的なアプローチとして、多くの企業で導入が進んでいます。
CBM実践のポイント
- 状態監視の適切な指標選定:温度や振動などの指標を基に、センサーやモニタリングシステムを導入
- データ解析と柔軟な保全計画:リアルタイムのデータ分析により、優先度を考慮した計画的なメンテナンスを実施
- 初期コストとROIの明確化:導入費用と投資回収率を明確にし、コスト効率の高い運用を目指す
- 継続的改善と教育体制:データや現場のフィードバックを活用し、保全手法を進化させ、従業員のスキル向上も推進
CBMを導入することで、設備の異常を早期に把握し、適切なタイミングでメンテナンスを実施する仕組みを構築できます。これにより、無駄なメンテナンス作業を削減し、設備の稼働率を最大化すると同時に、コスト削減と生産性向上を図ることが可能です。CBMの導入は、企業にとって次世代の保全体制を築くための重要な一歩となるでしょう。
状態基準保全(CBM)を始めるなら設備保全の一元管理に最適なMONiPLAT
CBMの導入を成功させるためには、データ収集から分析、メンテナンス計画までを一貫して管理できるシステムが不可欠です。MONiPLATは、設備の定期点検と状態監視を一元管理できるクラウドシステムとして、CBMの導入・運用を強力にサポートします。
MONiPLATには、時間基準保全(TBM)を管理する「MONiPLAT TBM」と、状態基準保全(CBM)をサポートする「MONiPLAT CBM」が組み込まれており、定期点検と状態監視を統合的に管理できる点が最大の特徴です。これにより、TBMで計画的なメンテナンスを行いつつ、CBMで設備のリアルタイムな状態を監視することで、両者の情報を総合的に活用し、最適なメンテナンス戦略を実現します。
また、MONiPLATはスマートフォン対応のため、現場での迅速なデータ入力や点検が簡単に行えます。CBMの導入によるリアルタイムの設備監視に加え、TBMによる計画的な点検も可能となるため、潜在的な問題を早期に発見し、無駄なメンテナンスを削減しながら、設備寿命の延長とコスト削減を両立できます。
MONiPLATのTBM機能は20設備まで無料で登録でき、アプリを使って簡単に設備点検を始めることができるため、初期投資を抑えつつ効果的な設備保全を実現したい企業に最適です。CBMの導入を検討している企業も、ぜひMONiPLATの一元管理システムをご活用ください。