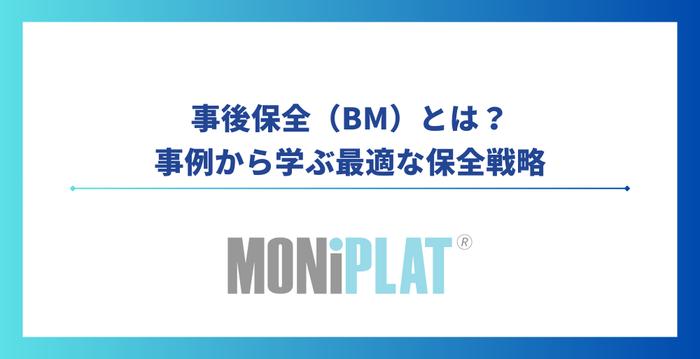
【2025年最新】事後保全(Breakdown Maintenance:BM・BDM)とは?事例から学ぶ最適な保全戦略
事後保全は設備が故障してから修理や交換を行う保全手法です。予防保全や予知保全など、他の保全手法に比べて初期導入のコストを抑えやすい一方で、突発的な故障による生産停止のリスクも伴います。
製造業やインフラ管理において、この手法が適しているケースを正しく理解することは、効果的な設備保全戦略の構築に欠かせません。本記事では、事後保全の基本情報から採用すべき状況、他保全手法との違い、さらには実際の成功事例まで網羅的に解説します。最適な設備保全を目指すための実践的なポイントを学んでいきましょう。
事後保全(BM)の基本情報と種類
事後保全は、設備が故障してから対応を行う「リアクティブ型」の保全手法です。この手法は、他の保全手法と異なり、予防的なメンテナンスを実施せず、設備のトラブルが発生した際に修理や交換を行うことが特徴です。
JIS(日本工業規格)では以下のように記載されています。
設備に故障が発見された段階で,その故障を取り除く方式の保全
一見すると「故障してから対応する」という考え方は非効率に見えるかもしれませんが、設備の重要度やRAKYを基に、適切な箇所に導入すればコスト削減や運用効率の向上につながる可能性があります。この章では、事後保全の概要とその種類、さらに対応する故障タイプについて解説します。
出典:[ JIS(日本産業規格) / 2021生産管理用語 ]
事後保全(BM)の概要と設備保全全体における位置付け
事後保全は、設備保全全体においてもっとも基本的な保全手法として位置付けられています。設備が稼働中である限りメンテナンスが不要なため、初期導入コストがかからず、特に予算が限られている小規模な事業や、設備停止が事業に大きな影響を与えない場合に採用されることが多いです。
ただし、故障後の修理により突発的なダウンタイムが発生するため、事後保全単独での運用は生産性や安全性を損なうリスクもあります。そのため、事後保全は予防保全や予知保全と組み合わせた形で採用されることが一般的です。
またRAKYを用いることで、設備の重要度や故障リスクを評価し、事後保全を適用すべき箇所を明確にすることができます。このプロセスにより、設備全体の保全効率を最大化することが可能です。
事後保全(BM)の種類と対応する故障タイプ
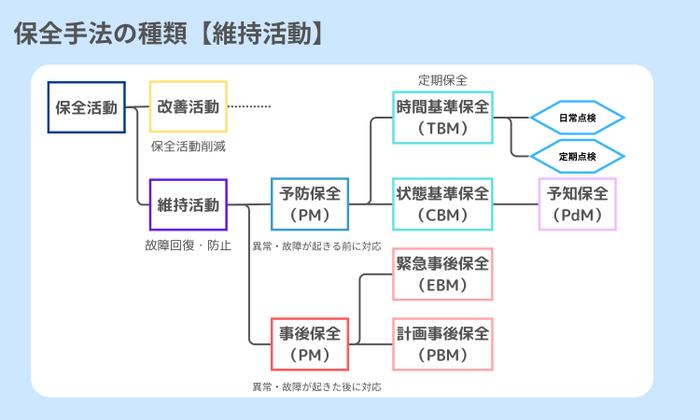
事後保全は、その運用形態や目的に応じて2つの主要な種類に分類されます。さらに、それぞれの種類は特定の故障タイプに対応するため、設備や運用環境に合わせた適切な選定が重要です。
緊急事後保全(Emergency Breakdown Maintenance:EBM)
緊急事後保全は突発的な故障に対し、迅速に対処するための保全手法です。予期せぬトラブルが発生した際、迅速な修理や交換を行うことで、設備停止の影響を最小限に抑えることを目的としています。
たとえば、電気系統のショートやモーターの完全停止など、生産ラインの中核を担う重要設備に大きな影響を与える可能性があり、設備の停止が事業に重大な影響を及ぼす場合に採用されます。
このような設備が完全に動作を停止するような重大な故障は「機能停止型故障」と呼ばれることもあり、緊急事後保全はこうした状況で迅速に復旧を図る手段として採用されます。
緊急事後保全の主な特徴は以下の通りです。
- 故障時に迅速な対応を可能にする緊急対応チームの設置
- 故障頻度の高い部品の予備在庫の確保
- 修理プロセスのマニュアル化と従業員トレーニングの実施
緊急事後保全は、特に生産に与える影響が大きい設備に対して適用されることが多く、対応の速さと柔軟性が求められます。
計画事後保全(Planned Breakdown Maintenance:PBM)
計画事後保全は、故障後の修理や交換作業をあらかじめ計画しておく手法です。予備機や代替設備が用意されている環境では、故障の発生時に即座に交換対応を行い、業務の影響を最小化することが可能です。
たとえば、ポンプの流量が低下している場合や、ベアリングが摩耗して振動が増加している場合など、非稼働時でも事業に影響が少ない設備や、修理が簡易である装置が該当します。
このような設備の性能は低下しているが、運転が継続可能な状態の故障は「機能低下型故障」と呼ばれることもあり、計画事後保全はこうした状況で設備稼働中に予備機や代替品を準備し、計画的に修理や交換を行うことで設備の安定性を確保します。
計画事後保全の主な特徴は以下の通りです。
- 故障リスクを前提とした計画的な対応
- 予備機の使用により業務継続を確保
- コスト効率を重視したリソース配分
計画事後保全は、予備機が用意されている設備や、修理に時間を要するが生産に大きな影響を与えない設備に適しています。
まとめ
事後保全は設備が故障した後に対応する受動的な保全手法で、初期コストを抑えられる反面、突発的なダウンタイムのリスクが伴います。緊急事後保全(EBM)は重大な故障に迅速対応する手法であり、計画事後保全(PBM)は予備機を用意して計画的に対応する手法です。それぞれの特徴を理解し、設備の重要度や運用環境に応じた適切な選定が重要です。
設備保全の目的と手法の選定基準
設備保全は設備の稼働を安定させ、生産性を向上させるために欠かせないプロセスです。しかし、保全手法の選定を誤ると、過剰なコストや不必要なメンテナンス作業が発生し、企業の経営資源を無駄にしてしまう可能性があります。そのため、リスクと費用対効果を考慮した保全戦略の策定が重要です。
この章では、保全手法を適切に選定するための基準であるRAKYと事後保全が採用されるべき状況について解説します。
RAKY(リスクアセスメント・危険予知活動)の重要性
RAKYは設備保全の手法選定において重要な役割を果たします。この評価プロセスでは、設備の重要性や故障リスク、影響範囲を総合的に分析し、最適な保全戦略を導き出します。
RAKYを活用することで、リスクの高い設備には予防保全を、リスクが低い設備には事後保全を適用するといった柔軟な保全戦略を構築できます。RAKYの評価プロセスでは、以下の項目が考慮されます。
リスクの発生可能性
設備が故障する頻度や兆候を評価します。故障頻度が高い場合、事前に対応できる予防保全や予知保全を採用することで、突発的な故障を未然に防ぐことが推奨されます。
故障時の影響範囲
故障が生産ライン全体や事業に与える影響を評価します。たとえば影響範囲が限定的な設備の場合、事後保全が現実的な選択肢となることもあります。
一方で、重大な影響を及ぼす可能性がある設備には、リスクを軽減する手法を選定する必要があります。
設備の重要性
設備が事業の中核を担っているのか、それとも補助的な役割を果たしているのかを分析します。中核設備の場合、予防保全は欠かせませんが、補助的な設備であればコスト面から事後保全の採用が可能です。
保全コストと費用対効果
事後保全(BM)を採用するべき状況
事後保全は、リスクが比較的低い設備や故障しても生産に大きな影響を与えない設備に適した保全手法です。RAKYの評価結果に基づき、以下のような条件下で事後保全を採用することが推奨されます。
設備の重要度が低い場合
生産ラインの補助的な設備や、一時的な停止が全体の生産性に影響を及ぼさない設備には、事後保全を採用することでコストを抑えられます。
迅速な修理や交換が可能な場合
故障時にすぐに交換可能な予備機が用意されている場合や、修理時間が短い設備では、事後保全が適しています。
ダウンタイムの影響が限定的な場合
故障によるダウンタイムが事業に大きな影響を与えない場合、計画的に事後保全を導入することで、初期コストを削減できます。
安全性や環境へのリスクが低い場合
故障が発生しても重大な安全リスクや環境問題を引き起こさない設備では、事後保全を選択することで効率的な運用が可能です。
事後保全を採用するための考慮ポイント
事後保全を採用する際は、以下のポイントに注意して計画を立てることが重要です。
- 故障時に迅速な対応が可能な体制を整える
- 故障リスクが予想される部品の予備在庫を確保する
- 設備の重要度や影響範囲を定期的に見直し、必要に応じて予防保全や予知保全に切り替える
事後保全はすべての状況で万能ではありませんが、適切に採用すればコスト削減や保全作業の効率化を実現できます。
まとめ
設備保全は、設備の稼働安定や生産性向上を目的とした重要なプロセスです。適切な手法選定のためには、RAKYによるリスク評価を活用し、設備の重要度や故障リスクを分析する必要があります。その中で事後保全はリスクが低く、故障時の影響が限定的な設備に適した手法で、迅速な対応体制や予備資材の確保を伴う運用が求められます。
事後保全(BM)のメリット・デメリット
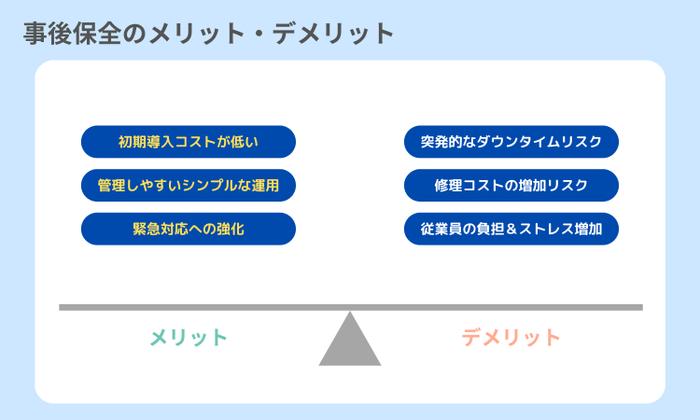
この章では、事後保全のメリットとデメリットを具体的に解説します。保全手法を選定する際の判断材料として、長所と短所をしっかり理解しておきましょう。
事後保全(BM)のメリット
事後保全は特定の条件下では、他の保全手法よりも効率的で費用対効果の高い選択肢となることがあります。以下に主なメリットを挙げます。
初期導入コストの低さ
事後保全では、故障が発生するまではメンテナンスを行わないため、初期コストを抑えられます。定期点検や予防保全のための人材や機材、インフラ投資が不要であり、設備投資を削減したい企業に適した手法です。
- コスト管理が容易:保全活動が発生するのは故障時のみであり、予算を緊急対応に集中させることができます。
- リソースの最小化:設備全体に対する継続的な投資が必要ないため、予算が限られている場合でも採用しやすいです。特に、Proof of Concept(PoC)段階で設備の導入をテストする場合に適しています。
簡単な運用で管理しやすい
事後保全では、設備が故障したときだけ対応するため、事前のメンテナンススケジュールや複雑な計画策定が不要です。管理の負担が軽減され、運用がシンプルである点も利点といえます。
- 効率的な対応:突発的なトラブル時に集中して対応するため、平常時は保全担当者の負担が少なく、リソースを節約できます。
- 計画負担の軽減:予防保全や予知保全と異なり、定期的なメンテナンス計画を立てる必要がないため、管理が簡単です。
リソースの集中化による緊急対応の強化
事後保全を採用することで、人的リソースや資材を故障発生時に集中的に投入できるため、緊急対応がスムーズになります。これにより、迅速な対応を可能にし、業務への影響を最小限に抑えることができます。
- 迅速な修理対応:故障が発生した場合、あらかじめ緊急対応の体制を整えておけば、すぐに対応可能です。
- 計画的な予備資材確保:故障リスクの高い部品や消耗品の在庫を予め確保することで、故障時の対応が迅速化されます。
事後保全(BM)のデメリット
事後保全には利点がある一方で、運用上のリスクやコスト増加の懸念も伴います。以下に主要なデメリットを説明します。
計画外のダウンタイムと生産損失
事後保全は計画外の故障に依存しているため、突発的なダウンタイムリスクが伴います。予期せぬ生産停止は生産性や納期の遅れに直結し、大きなビジネスリスクとなります。
- 生産停止リスク:主要設備が故障した場合、生産ライン全体が停止し、計画外のロスが発生します。
- 機会損失:生産ラインのダウンタイムにより、顧客への納品遅延や市場機会の喪失が懸念されます。
長期的な修理コストの増加リスク
事後保全では、設備が予期せぬタイミングで故障するため、高額な修理費用が一度にかかる可能性があります。特に故障が深刻な場合、部品交換や専門的な修理が必要となり、予算を超える出費が生じることもあります。
- 設備寿命の短縮:定期的なメンテナンスを行わないため、摩耗や腐食によって設備が早期に劣化するリスクがあります。
- 予測不能な出費:故障の規模やタイミングが予測しづらく、設備に対する継続的な管理が難しくなります。
従業員の負担増加と心理的ストレス
事後保全は突発的なトラブル対応が主となるため、従業員に負担がかかりやすく、特に夜間や休日の緊急対応が発生する場合、心理的なストレスが増大することがあります。
- 不規則な勤務:突発対応が求められることで、従業員が夜間や休日に対応を強いられることが増える可能性があります。
- ストレスの蓄積:急な対応を求められると、従業員のメンタルヘルスに影響が出る可能性があるため、ケアが必要です。
メリットとデメリットのバランスを考慮した導入
事後保全を導入する際は、設備の重要度や故障時の影響を評価し、メリットとデメリットのバランスを考慮することが重要です。また、突発的なダウンタイムへの対応や修理コストの管理が求められるため、他の保全手法との併用も検討する必要があります。
たとえば、主要設備には予防保全を適用し、重要度の低い設備に事後保全を導入することで、全体のメンテナンスコストを最適化できます。
まとめ
事後保全は初期コストを抑え、運用がシンプルで緊急対応力を強化できるメリットがあります。一方で、計画外のダウンタイムや予期せぬ修理費用の増加、従業員の負担増加といったデメリットも伴います。設備の重要度や影響を評価し、メリットとデメリットを考慮したバランスの取れた導入が重要です。他の保全手法と組み合わせることで、コスト効率と運用効率を最適化できます。
事後保全とその他の保全手法との比較
事後保全は、予防保全や予知保全などの他の保全手法と比較して、それぞれ特有の役割を持ちます。効果的な設備保全を実現するためには、これらの手法を単独で用いるのではなく、設備や生産体制に応じて組み合わせることが鍵となります。
予防保全(Preventive Maintenance:PM)との違い:安定稼働を目指した計画的なメンテナンス
予防保全は、設備が故障する前に計画的なメンテナンスを実施する手法です。この手法は、突発的な故障を防ぐことで、設備の稼働率を安定させることを目的としています。
特徴としては以下が挙げられます。
- 定期的な点検や保守作業により、設備の寿命を延ばし、ダウンタイムを最小限に抑える
- 時間や状態を基準に保全計画を立てるため、生産スケジュールを乱さず、安定した稼働を実現できる
事後保全との違いとしては以下が挙げられます。
- 事後保全と比較して初期導入や継続的な保全費用が高い
- 突発的な故障のリスクを軽減できる一方で、設備が予想よりも早く故障した場合、予防保全の計画が無効になることもある
予知保全(Predictive Maintenance:PdM)との違い:先進技術による故障予兆の監視
予知保全は、AIやIoTセンサーを活用し、設備の状態をリアルタイムで監視することで、故障の予兆を捉えて適切なタイミングで保全を行う手法です。最新技術を取り入れることで、より高度な保全が可能になります。
特徴としては以下が挙げられます。
- AIやセンサーを活用してリアルタイムの異常検知を実現
- 必要最小限の保全で、コスト削減と設備の稼働率向上を両立
事後保全との違いとしては以下が挙げられます。
- 事後保全に比べ、高度な技術や専門知識が必要
- 予知保全の導入は初期投資が大きくなる一方で、長期的にはコスト削減効果が期待できる
他の保全手法との補完関係を踏まえた検討ポイント
すべての設備に対して単一の保全手法を適用するのではなく、設備の重要性やリスクに応じて手法を組み合わせることで、効率的な設備保全を実現できます。
事後保全を補完するポイントとしては以下が挙げられます。
- 生産性に直結する主要設備には、予防保全や予知保全を適用
- 重要度が低く、故障時の影響が軽微な設備には、事後保全を採用してコストを抑える
具体例としては以下が挙げられます。
- 生産ラインの中核設備には予防保全を導入し、補助設備には事後保全を適用
- AIセンサーを用いて故障予兆をモニタリングし、異常検知時には事後保全で対応
まとめ
事後保全は予防保全や予知保全と比べて初期コストが低い一方で、突発的な故障リスクが高い特徴があります。予防保全は計画的なメンテナンスで安定稼働を実現し、予知保全はAIやIoTを活用して故障予兆を監視する先進的な手法です。設備の重要度や故障リスクに応じて、これらの保全手法を適切に組み合わせることで、保全の効率化とコスト最適化を図ることが可能です。
事後保全(BM)を含む設備保全の成功事例から学ぶ実践的なポイント
事後保全単独での成功事例は限られていますが、他の保全手法と組み合わせることで、設備の稼働率を向上させ、生産トラブルを削減する実績が多く見られます。
この章では、事後保全を中心に他の手法を補完的に活用した成功事例を紹介し、実践的なポイントを解説します。
自動車製造業A社:迅速な修理体制の整備による生産効率向上
とある自動車製造工場では、故障が発生した際の生産停止時間を最小限に抑えることを目標に、事後保全を中心とした迅速な修理体制を整備しました。この取り組みの一環として、専門の緊急対応チームを編成し、現場に即座に派遣できる体制を構築しました。
また、頻発する故障の原因となる部品を事前に在庫として確保することで、修理の効率化を図っています。さらに、故障対応を標準化するために、作業プロセスをマニュアル化しました。
この結果、誰が対応しても一定の品質とスピードを維持できる体制を実現しています。これらの施策により、生産ラインのダウンタイムが短縮され、稼働率の向上を達成しました。また、顧客への納期を守れるようになり、取引先からの信頼も向上しています。
航空会社B社:対応マニュアルと整備士トレーニングの強化で安全性と顧客満足度が向上
ある航空会社では、航空機の故障に迅速かつ的確に対応するため、事後保全を基軸にしながら、対応マニュアルの整備と整備士のスキル向上に注力しました。
故障が発生した際には、明確な手順に従って迅速な対応が行われるように対応マニュアルを整備しました。このマニュアルには、標準的な故障ケースごとに詳細な対応手順が記載されており、整備士が迷うことなく対応できる仕組みを構築しています。さらに整備士を対象に定期的なスキルアップトレーニングを実施し、対応力を強化しました。
この結果、故障から復旧までの時間が短縮され、航空機の定時運航率が向上しました。顧客満足度も向上し、安全性の確保が企業イメージの向上にも寄与しました。この事例は、事後保全と予防的なトレーニングを組み合わせた成功例と言えるでしょう。
エネルギー産業C社:データ分析と故障パターン学習で運転効率を改善
エネルギー産業では、発電所設備の故障による影響を最小化するため、事後保全に加えてデータ分析と予知保全を組み合わせる手法を採用しました。まず過去の故障データを徹底的に分析し、共通するトラブルパターンを特定。このデータを活用することで、再発リスクを低減するための予防措置を計画的に導入しました。
また、IoTセンサーやリアルタイムのモニタリングシステムを導入し、設備の状態を常時監視できる仕組みを構築しました。これにより、故障の予兆を早期に検知し、計画的な保全作業を実施できるようになりました。
これらの取り組みによって、運転効率が向上し、発電コストの削減にも成功しました。事後保全の迅速な対応力と予知保全の先進技術を組み合わせた優れたモデルケースと言えるでしょう。
まとめ
事後保全は他の保全手法と組み合わせることで、設備の稼働率向上や生産トラブル削減を実現します。迅速な修理体制の整備によるダウンタイムの最小化や、対応マニュアルとトレーニング強化による安全性と顧客満足度の向上、またデータ分析と予知保全を併用することで効率的な運転の実現など、さまざまな事例から、柔軟な保全手法の活用が重要であることが分かります。
事後保全(BM)を含む具体的な設備保全戦略の構築方法とステップ
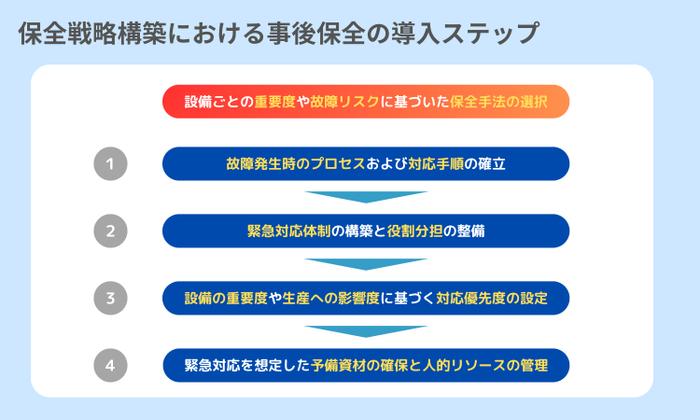
事後保全は設備保全全体の一部として位置づけられますが、効果的な運用には他の手法との組み合わせや戦略的な計画が重要です。
この章では、設備保全戦略の構築における事後保全の役割とその運用手順について解説します。
設備の重要度に基づく保全手法の選択
保全戦略を立てる際、すべての設備に同じ方法を適用するのではなく、設備ごとの重要度や故障リスクに基づいて保全手法を選択することが鍵となります。生産ラインの中核を担う主要設備には予防保全や予知保全を適用し、リスクが相対的に低い補助設備には事後保全を適用することが一般的です。
この選択を行う際には、RAKYなどの評価手法を活用し、設備の役割や故障時の影響度を明確にすることが推奨されます。
たとえば、頻繁に稼働する設備であれば、ダウンタイムの影響を考慮して積極的な保全手法を採用し、補助的な機器には事後保全を中心とした低コストな運用を検討することで、全体のバランスを取ることができます。
事後保全のプロセス設計と緊急対応体制
事後保全を含む保全戦略の構築には、明確なプロセス設計と緊急対応体制の構築が欠かせません。以下は、具体的な運用手順と体制の整備についての解説です。
故障発生時のプロセスと対応手順
事後保全の基盤となるのは、迅速な故障対応です。故障発生時には、以下のような手順を確立しておくことで、対応の効率性を高めることができます。
- 初動確認と緊急度評価:故障の確認後、設備の停止が生産に与える影響を迅速に評価し、優先度を決定します。このとき、他設備やシステムへの影響を考慮し、必要な緊急度で対処することが求められます。
- 原因の特定と修理計画の立案:故障原因を迅速に特定し、必要な部品や資材の手配を行います。原因特定には、過去のデータや履歴を参考にしながら、最適な修理方法を選定します。
- 修理の実施と再稼働確認:修理後、再度稼働確認を行い、設備が正常に動作することを確認してから通常の生産に復帰させます。この確認作業は、後続の故障を防ぐために重要なステップです。
突発対応の体制構築と役割分担の重要性
突発的な故障に対応するためには、あらかじめ役割を明確にした緊急対応体制を整えておく必要があります。以下のポイントが重要です。
- 役割分担の明確化:各メンバーの役割や責任を事前に定め、対応プロセスがスムーズに進むようにします。設備保全担当者や技術者が必要な対応を迅速に開始できる体制を整えておくことが重要です。
- シフト制と応援体制の導入:突発的な故障に備えて、シフト制を導入することで24時間対応可能な状態を維持します。夜間や休日の緊急対応には、あらかじめ応援体制を組んでおくことで、迅速な対応が可能です。
- 定期的な訓練とシミュレーションの実施:緊急時の対応力を強化するために、定期的な訓練やシミュレーションを実施し、迅速で的確な対応力を養います。
設備の重要度に基づく対応優先度の決定
設備の重要度や生産プロセスへの影響度に基づき、対応の優先順位を設定することは、効果的な事後保全運用の要となります。
- 生産プロセスへの影響度評価:生産ラインにおいて、故障が全体の稼働に与える影響を評価し、重要な設備は優先的に対応します。たとえば、生産のボトルネックになり得る主要設備は、他の設備よりも優先して復旧を図るべきです。
- 復旧時間とコストの見積もり:設備の重要度に応じて、復旧にかかる時間とコストを見積もり、費用対効果を考慮しながら修理計画を立案します。
- リスク評価に基づく対応計画の策定:事前にリスク評価を行い、設備の故障が発生した場合の影響範囲を特定し、最適な対応戦略を立てます。これにより、優先度を明確にした計画的な対応が可能になります。
予備資材と人的リソースの管理
事後保全を円滑に進めるには、予備資材の確保と人的リソースの管理が重要です。突発的な対応には、備品や部品の在庫状況、担当者のスキルレベルなども大きく関わります。
- 予備部品の在庫管理:故障頻度が高い設備に対しては、予備部品の在庫を事前に確保し、スムーズな修理を可能にします。特に、リードタイムが長い部品は計画的に在庫しておくことが必要です。
- 人的リソースの適正配置:緊急時に対応できる技術者や保全担当者を適切に配置し、突発対応におけるスキルアップを図ります。必要に応じて社内外のリソースも活用します。
まとめ
事後保全を含む設備保全戦略の構築では、設備の重要度や故障リスクに応じた保全手法の選定が重要です。迅速な故障対応を実現するために、明確なプロセス設計や緊急対応体制を整備し、役割分担や訓練を通じて対応力を強化します。また予備資材の確保や人的リソースの適正配置によって、効率的な運用が可能となります。その他保全手法と組み合わせた戦略的な運用が、設備保全の成功につながります。
事後保全(BM)を導入する際の注意点と課題
事後保全を導入する際には、特定の状況下での運用に適した戦略を練ることが重要です。この章では、事後保全の導入時に留意すべき課題について解説します。
緊急対応体制の構築と作業負担の調整
事後保全では突発的な故障への迅速な対応が求められるため、緊急対応体制の構築が欠かせません。この体制を整えることで、設備停止が生産に及ぼす影響を最小限に抑えることが可能です。シフト制の導入や役割分担の明確化により、スタッフが適切に対応できる柔軟な環境を作り出します。
さらにスタッフへの負担軽減を図るため、夜間や休日の対応方針を予め明確化し、業務を分散させる工夫も重要です。たとえば、トレーニングやシミュレーションを定期的に行うことで、緊急対応時のスキルを向上させつつ、心理的な負担を軽減できます。
設備寿命と修理コスト管理の重要性
設備が突然故障することで発生する高額な修理費用を抑えるには、事前の寿命予測とコスト管理が欠かせません。特に主要設備の修理費用は計画外で発生するため、企業の予算に大きな影響を与えることがあります。
設備ごとの寿命を評価し、必要に応じて更新計画を立てることで、コストの急激な増加を回避できます。また、突発的な修理費用に備えて予算枠を確保しておくことが、長期的なコスト管理の安定化に繋がります。
計画外のダウンタイムによる生産性への影響
計画外のダウンタイムは生産性の低下や納期の遅れなど、事業に直接的な悪影響を及ぼします。そのため、事後保全を導入する際には、故障時の影響範囲を正確に見積もることが重要です。
たとえばバックアッププランを策定しておけば、突発的なトラブル時でも生産活動を維持できます。また、設備の故障リスクとその影響を評価し、リスクの大きい設備には予防保全や予知保全を組み合わせることで、ダウンタイムの発生確率を低減させることが可能です。
他設備保全手法を組み合わせた多角的な設備保全
事後保全を効果的に運用するには、単独での採用だけでなく、他の保全手法との組み合わせが求められます。たとえば主要設備には予防保全を適用し、補助設備には事後保全を採用することで、全体の保全コストを最適化できます。
さらに予防保全や予知保全を組み合わせることで、事後保全の弱点を補い、設備全体の稼働率向上やコスト効率化が期待できます。国土交通省も、インフラメンテナンスの効率化のために予防保全への転換を推奨しており、事後保全のメリットを活かしながら長期的な戦略を検討することが求められます。
出典:[ 国土交通省 / 予防保全によるメンテナンスへの転換について ]
まとめ
事後保全を導入する際には、緊急対応体制の整備やスタッフ負担の調整が重要です。設備寿命の評価とコスト管理を行い、予算オーバーや計画外のダウンタイムによる生産性低下を防ぐ工夫が求められます。他の保全手法と組み合わせることで、事後保全の弱点を補いながら、設備全体の効率的な運用を目指すことができます。長期的な戦略と柔軟な対応力が導入成功の鍵です。
事後保全で設備の故障リスクを最小化し、生産効率を向上させましょう
事後保全は設備が故障した際に迅速に修理や交換を行うことで、効率的な設備運用を実現する保全手法です。リスク評価を活用し、設備の重要度や影響範囲を見極めて適切に運用することが、事後保全を成功させる鍵となります。
事後保全の実践ポイント
- 緊急対応体制の整備:役割分担を明確にし、シフト制や応援体制を導入して迅速な故障対応を可能にする。
- 予備資材の管理:故障リスクの高い部品の在庫を事前に確保し、修理作業をスムーズに進める。
- RAKYによる設備評価:設備の重要度やリスクを評価し、適切な保全手法を選定する。
- 他手法との組み合わせ:主要設備には予防保全や予知保全を採用し、事後保全と併用してコストとリスクを最適化する。
事後保全は設備の柔軟な運用を可能にする一方で、突発的な故障リスクへの迅速な対応が求められます。他の保全手法と組み合わせることで、コスト削減や生産効率の向上を実現できます。適切な戦略と計画をもって導入することで、設備保全の全体最適化を目指しましょう。